David Gilmour, business manager, Built Environment Services, SOCOTEC, visited the maintenance depot of a long-term rail client for their monthly depot monitoring assessment, as part of SOCOTEC’s services to keep them compliant.
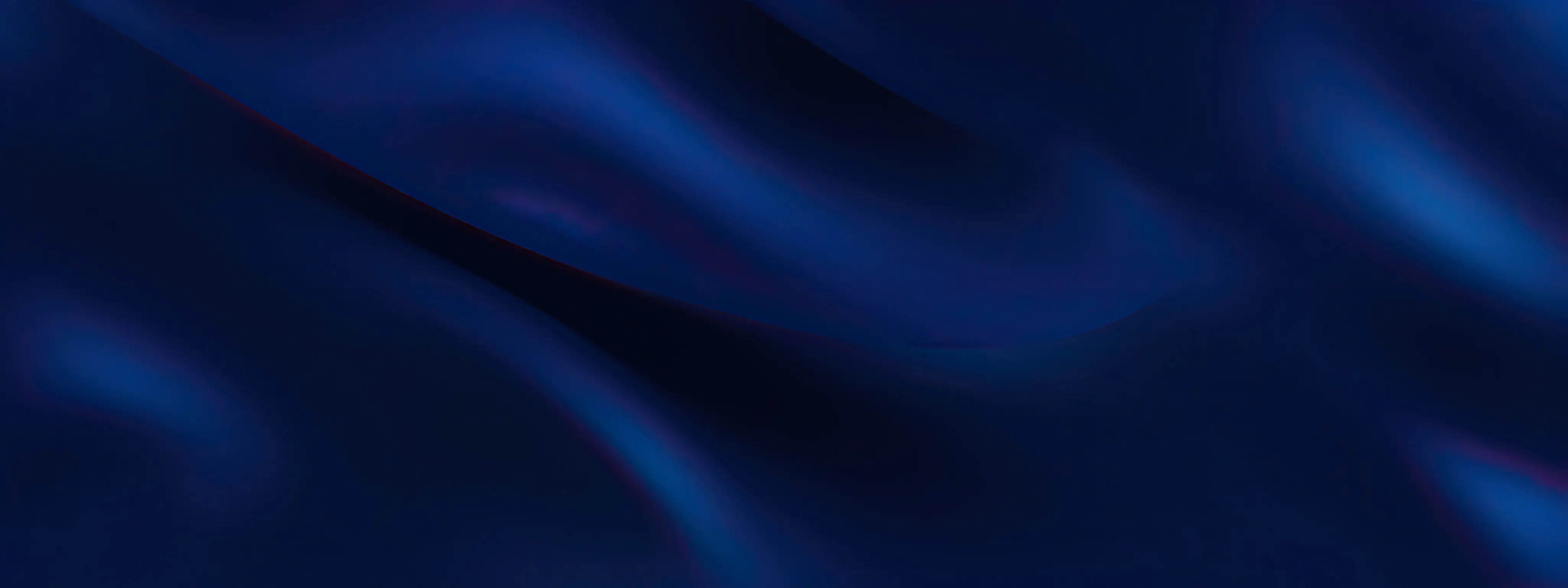
Here, David tells us about his day on site to share what goes on behind the scenes.
David, what’s your background with rail?
I’ve been working for the company for 16 years, mainly focusing on providing clients with technical services to ensure environmental compliance, operational risk reduction and also providing technical guidance. A large part of my experience would relate to water discharges and pollution control measures, such as trade effluent and surface water monitoring. However, other areas of water quality, such as drinking water and Legionella control, would also be routine.
Within my role, working with rail based clients take up around 50% of my time. As the rail industry has changed hugely over the years, it is an area which continually needs to conform to environmental legislation.
With my technical background in Environmental Science, I work alongside our rail clients to help enhance their understanding of legislation and provide solutions for them to ensure that they comply. Being on site is a very enjoyable part of my job as I get to build relationships with clients by talking with them one-to-one about the challenges they face. I also get to see the changes first-hand, such as new facilities, rolling stock or infrastructure, and then demonstrate how SOCOTEC can support them through our technical support and site services.
What’s involved with a rail depot visit?
A general visit to a depot occurs monthly. However, the frequency of visiting certain sites can vary depending on the size of depot, the specific facilities each depot has, the overall operational risk posed that could impact on rail operations and the environmental risk that could subsequently cause environmental impact from each site. Essentially, we are checking multiple features and the facilities of the site to make sure everything is running as effectively as possible.
This particular depot is a full-scale engineering site with maintenance and cleaning facilities. Typically, it receives between 80-100 passenger trains on a daily basis. My job is to inspect and monitor behind the scenes to ensure the features and facilities of the site run effectively which then enable the depot operations to function at the maximum level, while complying with regulations set by Scottish Water, Scottish Environment Protection Agency (SEPA) and the recognised rail industry guidance and best practice. Our services help to reduce costs for the client, minimises the impact to the environment as well as helping to proactively manage potential operating risks.
When you arrived on site, where did you start?
After signing in at the reception and gearing up with the appropriate PPE, the first task on this site is to visually inspect a surface water outfall and obtain samples of the discharge to take to the laboratory for analysis. This particular site has a total of seven surface water and trade effluent sampling locations. Our objective is to identify the final outfall quality of these locations, but to also look at areas within the site drainage which may be contributing to the overall impact.
Depending on where the water is discharged, it needs to meet the criteria laid out by Scottish Water or SEPA. Originating in the late 1800s, this particular site has areas that are heavily contaminated from fuel spillages dating back to the 1960’s and 1970’s – when environmental monitoring wasn’t a focus. Our tests ensure the client is meeting these guidelines and identifies where remedial action may be required.
The oil separator receives surface water combined from two different sources. One of the sources is an underground culvert which can receive historic oil contamination. At the end of the culvert, there is a vertical metal plate slotted in just below the water level which acts as a simple but effective oil retention feature.
With several individual chambers which reduce oil levels at each stage, the main oil separator acts as the final and most effective feature by ensuring that oil levels in the discharged water comply with the conditions of the SEPA discharge license.
Being in the field for 16 years, I have a lot of on-site experience determining if a water discharge is compliant or not, allowing the client to be informed and who can then take urgent action. This can also be applied to other areas of sampling within the depot visit. Of course, in addition to the visual inspection, samples are also analysed by ESG’s accredited laboratories to determine if the sampled locations meet the criteria outlined by SEPA.
We’ve covered surface water discharges, what about the ever-glamorous trade effluent?
A depot visit usually includes sampling trade effluent from large, industrial separators. Although generally larger than surface water separators with a more mechanical design, they work with the same principal by taking in a flow of contaminated trade effluent. This passes through each filter and chamber to retain and reduce contaminants such as oil and solids.
From these separators, the effluent releases into the foul sewer system which is regulated by Scottish Water. Our laboratories determine the various parameters set out by the discharge consent such as oil, pH, suspended solids, chemical oxygen demand and biochemical oxygen demand. By comparing our analytical results with the limits set out by Scottish Water, we can ensure the effluent discharge complies with the consent conditions.
What about the trains themselves?
Ultimately, the maintenance and operation of the trains is the core depot function. A depot visit also includes inspection and obtaining samples from facilities such as train wash systems, coolant systems and fuel storage systems. Good quality diesel fuel is always of paramount importance to ensuring the trains are fit for service. The fuel must be clean, without any elevated water, particulates or microbiological contaminants. All of these contaminants can have a detrimental impact on the train engine when in service - with very expensive consequences, and poor publicity, if an engine failure occurs!
We also sample engine coolant to determine if the glycol concentration meets the engineering requirements for the various types of rolling stock. Deionised water is also monitored from the various purification cartridges to identify if the pure water is fit for use in the battery system. We are able to trend the analytical results from all these types of systems for clients, which allows us to determine where there are potential issues. From this, we can provide the required guidance or solution to the client to prevent an operational risk.
With our inspection and analytical services, we’re offering the client peace of mind by managing the potential operational risks to guarantee optimum output from the depot productions, increased reliability of the trains and reduction of disruptions further down the line.
In the current climate of the rail industry, one of the key issues to train operators and the travelling public is train presentation. Presenting a clean train, both internally and externally, is a real priority. Across the UK, there are a large number of train wash systems which SOCOTEC are involved in monitoring and assessing to ensure exterior (body-side) cleaning is efficient and meets the industry standard.
Our testing allows us to analyse the operational efficiency of an individual wash system. We can also monitor to determine the concentration of each cleaning chemical used in the washing process and, from those test results, feedback to the client on any adjustments that are needed to boost the wash performance.
Achieving the correct dosing concentration is important for several reasons. Each chemical has a unique range to be dosed but also an optimum working strength which is beneficial to the cleaning efficiency. Low chemical dosing may result in a reduced wash performance causing poor train presentation, while elevated dosing also causes issues. Excessive chemical dosing may lead to a detrimental effect on trade effluent quality which raises the risk of discharge consent failure. It also reduces stock levels at a much quicker rate, leading to higher running costs. By ensuring the right dosing concentrations are achieved, the client is assured that the operating performance of the wash system is at the optimum level, they are working on the most cost effective setting by minimising waste and the environmental impact is reduced.
You have 15 years’ experience of Legionella risk assessment – does this crop up on site?
Legionella can be a risk on any site and, as this particular depot contains a train wash system, it must be managed and assessed in line with the current HSE guidance. Today, we won’t be conducting a full risk assessment of the wash system; however, we are taking water samples from three locations to provide information on the condition of the overall system. The samples will be taken from the:
- Emergency Shower
- Emergency Eye wash
- Final rinse
The emergency shower and eye wash outlets are used infrequently because of what they’re intended for, so the risk of legionella can be high if the outlets are not flushed, monitored and managed. As SOCOTEC monitor each month, we can identify any adverse results or poor conditions to the client and ensure that the water system is safe and doesn’t pose any risks.
Thank you for your time. As a parting question, do you have a favourite bit to the day?
Being on site can be a challenging place to work, but there is a degree of satisfaction in conducting the assessments, identifying areas of concern and discussing with clients on where improvements are needed. I like to think that clients rely on SOCOTEC to enable them to move forwards as a business and that we help them to meet their responsibilities. I like to offer interpretation on the site observations and analytical results, by recommending solutions with a proactive approach to suit the individual client’s needs. Changes implemented on a site, seeing progress and receiving positive feedback from clients are all very rewarding aspects of the role.
If you have a favourite part to being on a rail depot, share a comment below or get in touch.
Want to find out more about SOCOTEC's rail services?
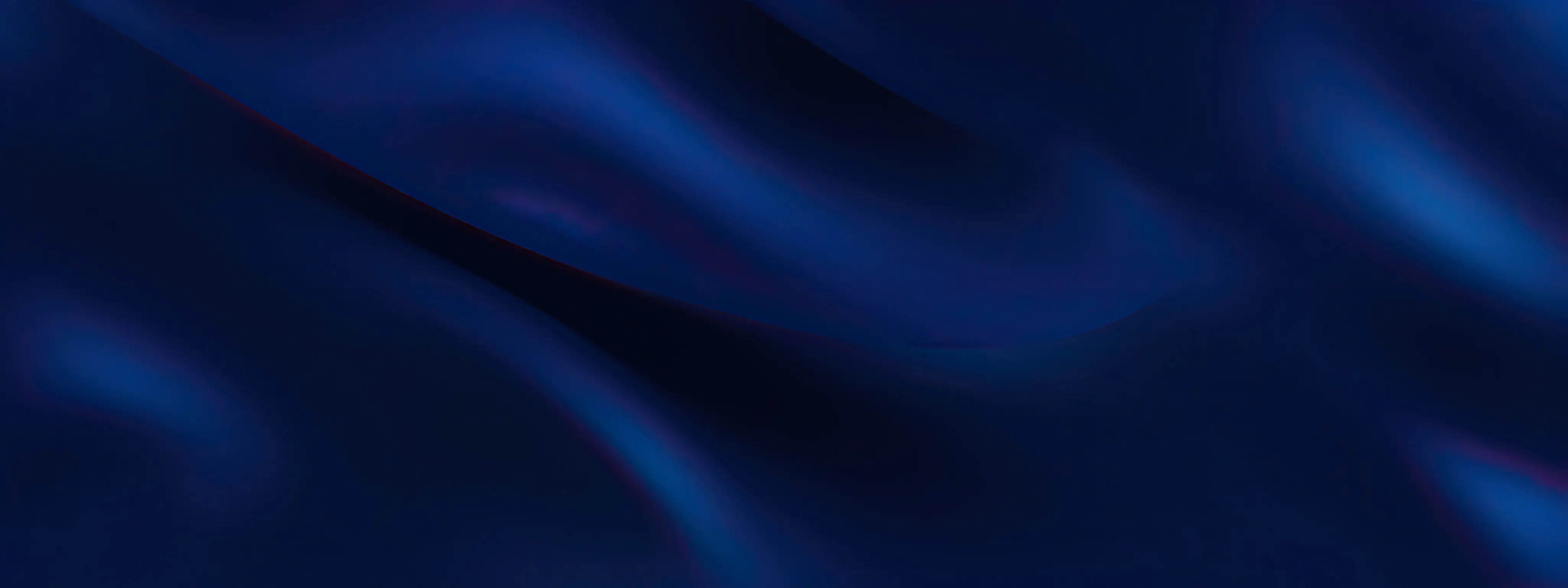
You might also like
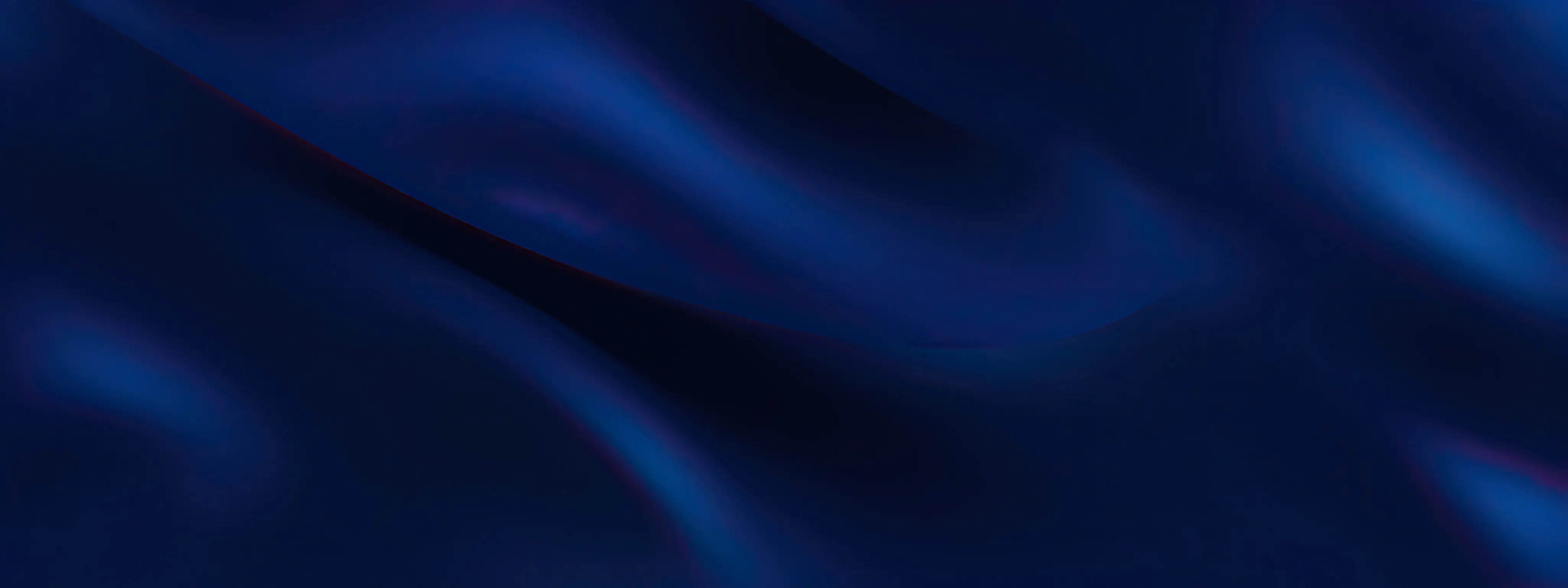
Add new comment