Employers in the UK must risk assess and manage employee exposure to electromagnetic fields (EMFs) in order to comply with the Control of Electromagnetic Fields at Work Regulations 2016 (CEMFAW). Many employers may not know where to start and will therefore choose to outsource the risk assessment process, but this can be relatively simple to complete in-house.
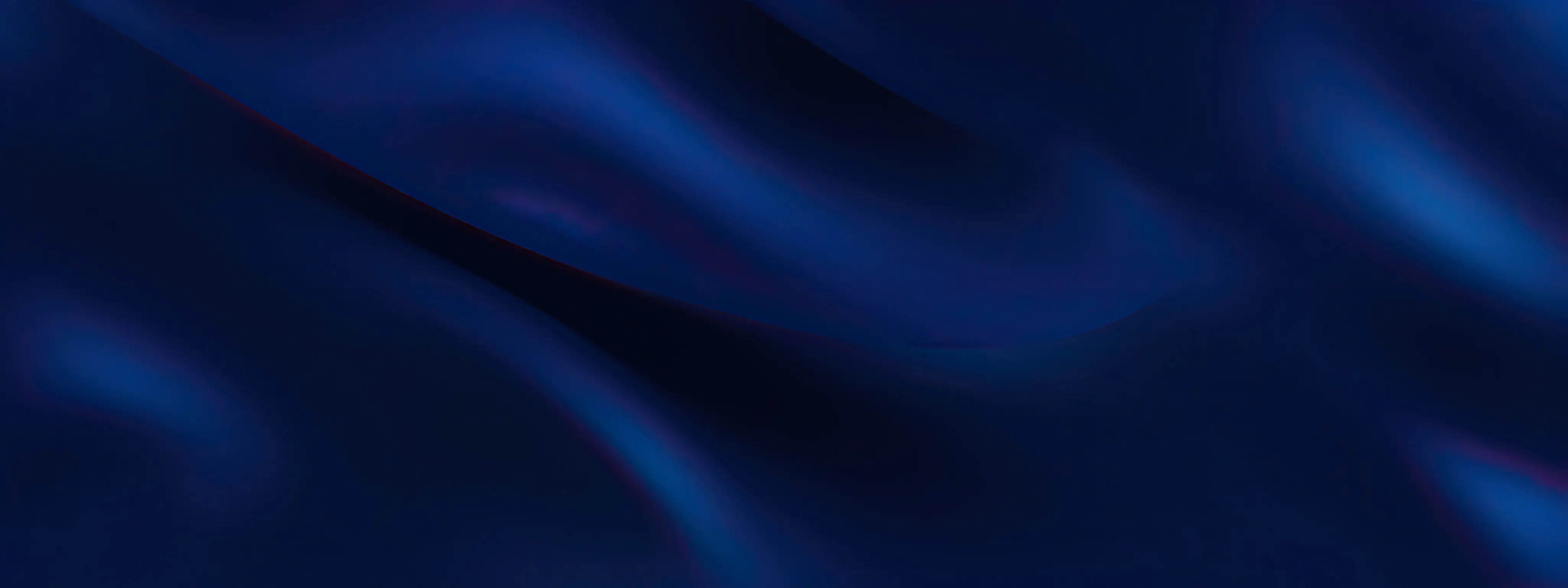
Many employers may not know where to start and will therefore choose to outsource the risk assessment process, but this can be relatively simple to complete in-house. In fact, in the majority of cases, there is no need to take any measurements because the risks posed are known to be insignificant, are covered by current risk assessments or are easily managed.
Whether the assessment is outsourced or completed in-house, the two most important areas to ascertain in order to kickstart the process are who is at risk and where these risks are located.
Where are the risks?
EMFs are created anywhere electricity is generated, transmitted or used. They can be created intentionally, such as in broadcasting, telecoms and radar, but these have been managed effectively for many years and are unlikely to need any further work under CEMFAW.
For most industries, EMFs of concern will often be those created unintentionally by processes that have a high electric current flow, such as resistance welding, arc furnaces, electrolysis and electricity supply (eg cables, busbars, switchgears). Many industries also use high-powered magnets for metal detection and magnetising. In premises visited by SOCOTEC assessors, the highest EMF levels for equipment accessible to employees have been associated with:
- Industrial motors and fans of various sizes and their power cables
- Welding sets
- Handheld power tools such as angle grinders (both mains and battery powered)
- Portable isolation transformers for 110 V supply.
To find out where the potential risks lie within the business, there is a useful table on page 24 of the Non-binding guide to good practice, Volume 1: Practical Guide, an excerpt from which is shown below.
Going through the entire table with an experienced maintenance engineer to identify which sources can be found on site – and where – is a good way to start the assessment. If there is nothing on site that has been recorded as a ‘yes’ in the list, the levels of EMFs are considered safe, the assessment can be recorded and a date set for review.
SOCOTEC also provides a handy guide on the requirements for specific EMF assessments in relation to common work activities, equipment and workplaces.
Who is at risk?
Anybody who needs to go near the EMF sources is potentially at risk. However, some employees are more at risk than others, and these are referred to as ‘workers at particular risk’. This includes:
- Employees who have active medical implants such as pacemakers and cochlear implants
- Employees who have passive medical implants such as artificial joints, pins and plates
- Employees with body-worn medical devices such as hormone infusion pumps
- Employees who are pregnant
By referencing the table above, it becomes clear that workers at particular risk – especially workers with active medical implants – are more likely to require control measures putting in place than other employees. Therefore, employers not only need to know who will be close to the strongest EMF sources, but they will also require an ongoing process in place to identify workers at particular risk. Employees and visitors need to be made aware of what these risks are, how to identify whether they are deemed to be at particular risk and the action that needs to be taken if this is the case.
Assessing the risk
If employers have determined that the levels of EMFs might not be safe, the next step in protecting their staff is to assess the level of risk. This is usually done by comparing the strength of the EMFs emitted by the sources against the Action Levels provided in the CEMFAW Regulations or, for workers a particular risk, referring to a set of much stricter limits known as ICNIRP 98 levels. There are a few different ways of finding out the strength of the EMFs:
- The manufacturer – newer equipment may indicate this via the CE marking, or the manufacturer might need to be contacted
- Industry standards and guidance
- The EU non-binding guides to good practice
- HSE guidance
- Taking direct measurements
The legislation has been written to minimise the need to take direct measurements, as long as the employer is prepared to put a bit of work into finding out the typical levels for their equipment. There are, however, some advantages to taking measurements: older or purpose-built equipment might have no EMF emission data and may no longer conform to typical levels; safe distances can easily be ascertained, allowing exclusion zones to be created, and lots of different equipment can all be checked quickly and easily as opposed to spending hours on research.
The measurement instruments cover a wide spectrum of EMFs and give a ‘weighted peak’ result as a percentage of the relevant Action Level or the ICNIRP 98 level as required, so it is immediately clear whether employees are likely to be exposed to high levels of EMF and at what distance this dissipates to a safe level. Usually this distance is very short, measured in centimetres rather than metres.
Taking action
If the initial risk assessment shows that there are risks to employees, an action plan is needed. In most cases, this will be a combination of signage and enforcing distance between the employer and the source, such as by guarding, setting exclusion zones and possibly rerouting walkways. For workers at particular risk, this may mean a slight change to their working layout or their actual job role.
Many actions will be self-explanatory – for example, if an employee has a medical implant such as a pacemaker, they should not keep things like mobile phones close to the implant and should avoid going near strong magnets such as metal detectors. If an old powered hand tool is generating much higher levels than a newer equivalent, workers should dispose of the old one and purchase a new one if required. Like any risk assessment, there is a requirement to give relevant training and information to employees and visitors, ensure that the action plan is acted upon and set a review date.
Example warning signs
As part of an employer’s action plan, appropriate warning signs need to be put in place in and around areas bordering the EMF source, indicating the nature of the hazard posed. Staff coming into contact with EMFs should therefore familiarise themselves with the below signs in line with good working practice. These are referenced within the Non-binding guide to good practice, Volume 1: Practical Guide:
In summary
The aim of this blog is to demonstrate that risk assessments for EMFs do not need to be onerous, and it is worth starting the process in-house before deciding whether measurements and/or outside help are needed. The process consists of:
- Identifying and locating the risks using the table in the Non-binding guide to good practice, Volume 1: Practical Guide
- Ongoing identification of ‘workers at particular risk’
- Finding out the EMF levels, either through research or measurement
- Comparing EMF levels to the relevant Action Levels or ICNIRP 98 values
- Making and acting on an action plan
- Recording the assessment and setting a review date.
Further reading
There is plenty of free guidance available to help employers complete an EMF risk assessment. For more detail on the responsibilities of the employer, refer to HSE guidance HSG281: Electromagnetic Fields at Work, while for case studies and further information, the Non-binding guide to good practice for implementing Directive 2013/35/EU publications include Guide for SMEs, Volume 1: Practical Guide and Volume 2: Case Studies.
Should you need any assistance with your EMF exposure risk assessment, SOCOTEC are able to provide a market-leading service that supports organisations in assessing, measuring and managing electromagnetic field sources.
Want to find out more about SOCOTEC's EMF assessments?
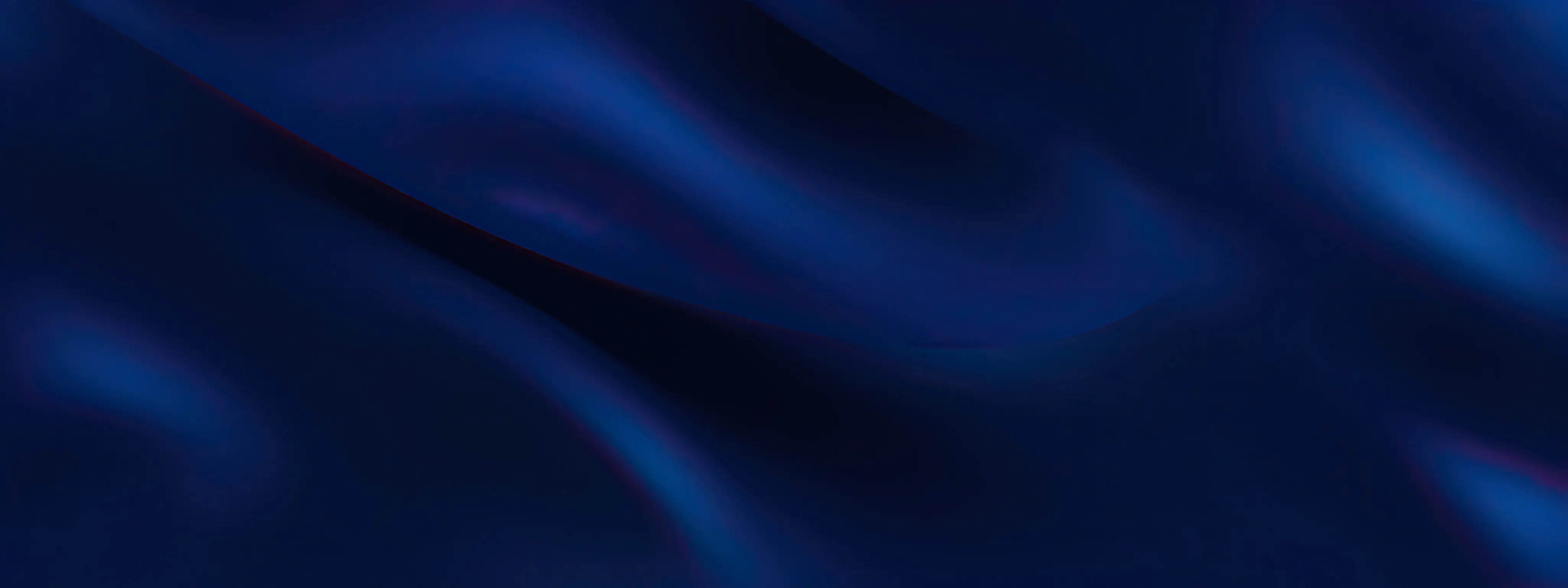
You might also like
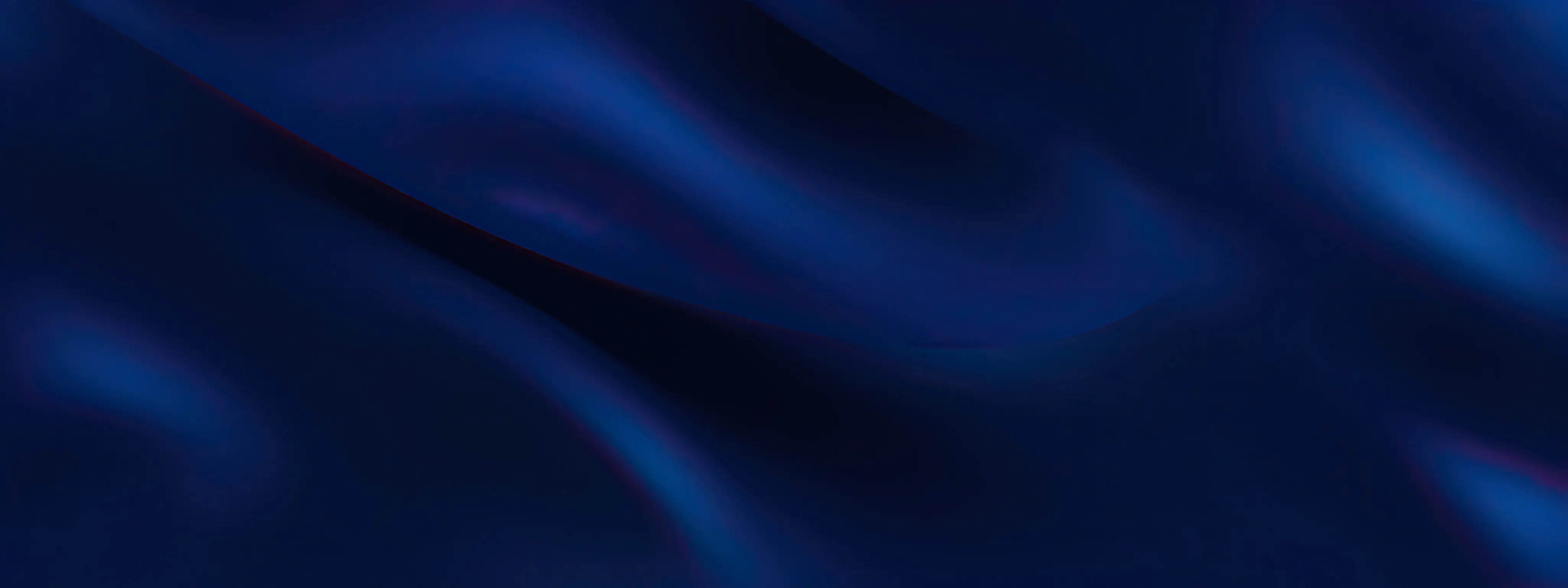
Add new comment