Food production requires a significant volume of water with around 25,000 litres being required to grow and produce a day’s supply of food for a family of four.
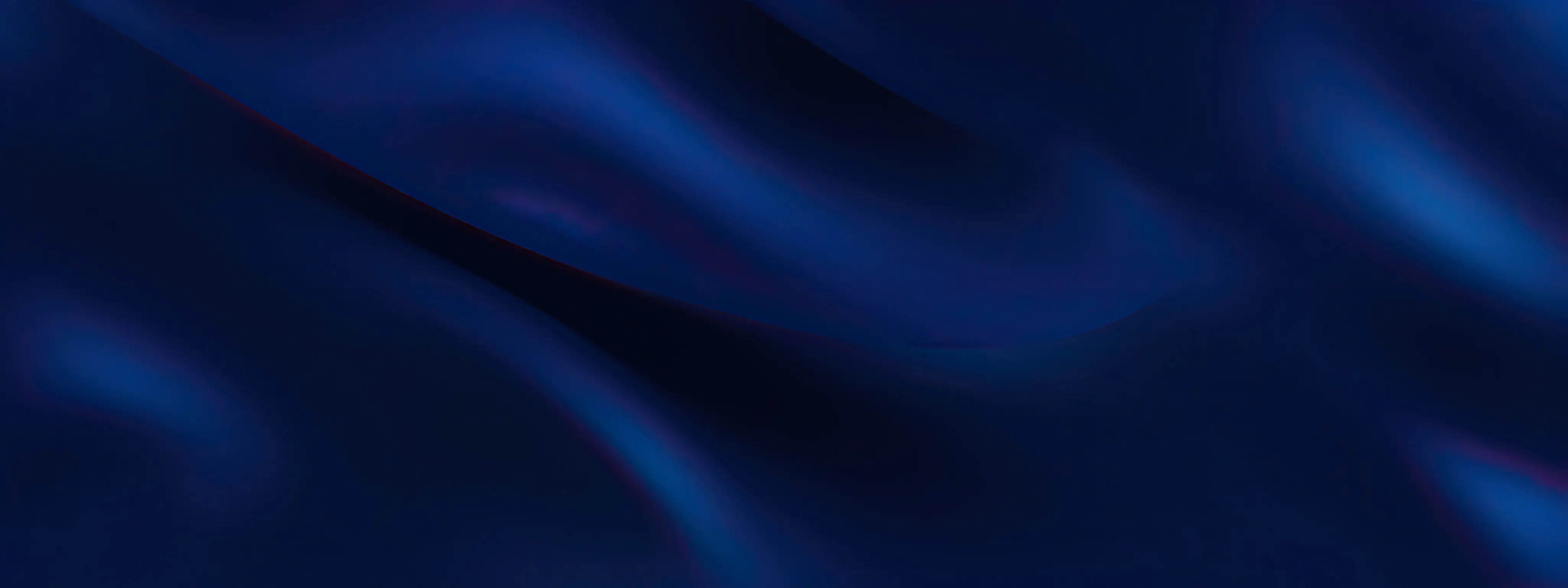
In order to guarantee safe food production and limit its environmental footprint, the food and beverage industry is forced to adopt a proper water management strategy utilising advanced treatment technology to achieve water savings and zero water discharge solutions.
The total volume of all water in the world has remained constant for thousands of years - with only approximately 2.5% of this total present as fresh water. The majority of this fresh water (circa 68%) is locked up in glaciers and ice caps leaving less than 1% of all water available as fresh water to support people, plants, trees and many other forms of life.
Food production requires a significant volume of water with around 25,000 litres being required to grow and produce a day’s supply of food for a family of four (Save the Water, 2019). With the growth in human development and population numbers, the value of water as a precious and finite resource is being increasingly recognised, especially in the food manufacturing industry which is heavily reliant upon it. In order to guarantee safe food production to an ever growing population and limit its environmental footprint, the food and beverage industry is forced to adopt a proper water management strategy utilising advanced treatment technology to achieve water savings and zero water discharge solutions.
There is an increasing trend of food and beverage manufacturers focusing on their water footprint both as a means of controlling operating costs and minimising environmental impact. Increasing costs of process water and wastewater discharge tariffs, stricter environmental legislation, progressing water stress and rising social awareness are forcing manufacturers to adopt water conservation programs and implement water re-use as well as closed loop water systems to achieve operational savings in both energy and water.
Recent research in food and beverage processing has shown that 66% of non-product water is used in Cleaning in Place (CIP) and heat exchangers such as cooling towers (Schug, 2016). The remaining one-third is split between manual cleaning, sanitation and miscellaneous utility demands.
Practices in re-usable bottles, kegs and containers in the beverage industry vary substantially. In some cases, water usage is as high as 45 litres per litre of product packaged. Optimal use of cleaning agents and effective wash and water recycling systems can reduce this significantly.
Water and wastewater treatment companies are developing new strategies in combining new and established treatment technologies together with eco-friendly chemical products to assist the food industry in meeting these objectives.
CIP Cleaning and Disinfection
Plant and equipment cleaning, particularly in the beverage industry, has traditionally been the major source of fresh water usage (WRAP, 2001). Using products such as Ozone as cleaning and disinfection agents provides opportunity for increased recycling and re-use of water – resulting in reduced water usage, waste discharges and environmental impact.
The use of Ozone in process water systems allows systems to be sterilised with minimal disruption and without draining or flushing. Typical processes using chemical disinfectants or heat sanitisation would require 12-24 hours outage time as well as complete drain down and flushing of the system. To achieve similar results using ozone requires less than 2 hours outage time with no draining required.
Root Vegetable Washing and Hydrocoolers
Developments in cyclone dirt separation filtration technology are providing benefits in vegetable and fresh produce washing by allowing greater re-use of water as a result of maintained cleanliness of the water systems. Therefore, reduced water consumption and improved handling of waste material can be achieved.
Recycling Waste Water from CIP, Processing & Cooling Towers
Reverse Osmosis & Membrane Filtration
Greater understanding in the design of Reverse Osmosis systems focussing on water footprint allows for significant reduction in waste water and increased membrane life. Typically Reverse Osmosis units have discharged 25-50% of input water as a waste stream. New developments and design allow this to be reduced to less 10% in most cases. This technology can also be applied to existing plant with minimal modification.
The use of Ultrafiltration and Reverse Osmosis in providing a positive barrier to suspended solids, bacteria, viruses, endotoxins and other pathogens provides opportunity for recycling water for clean applications in food and beverage manufacturing
Electro-deionisation
New developments in Electro-deionisation target the desalination or purification of impaired water or water with elevated salt levels. This technology increases the energy efficiency and reduces the water footprint of traditional purification process and allows a wider range of applications - ideally suited to water recycling in the food and beverage industry.
Electrolytic Disinfection
The use of electrolysis to generate disinfection products from the natural minerals in water provides an opportunity for extending the use of water, recycling and maintaining water hygiene with minimal environmental impact.
The range of water treatment options available to the food and drink industry can support them in reducing water consumption, with varying methods available depending on the individual objectives of the food/drink processor.
- Read our case study: Efficient Sanitation Methods for Timothy Taylor Brewery
- Read our article: Thinking Beyond Chemicals for Sustainable Fresh Produce Sanitation
References
Save the Water (2019) Education Resources, Water Facts [accessed 29 May 2019] http://savethewater.org/education-resources/water-facts/
Schug, D. (2016). Reducing water usage in food and beverage processing.
Szyplinska, P. Food and beverage industry focuses on water footprint and greater sustainability Industry Analyst for Environment (Water) Markets at Frost & Sullivan
WRAP (2001) Case Study: UK Drinks Sector, Water efficiency
WRAP (2001) Case Study: UK Drinks Sector, Resource efficiency in the UK brewing sector.
Want to find out more about how we can support your food and beverage organisation?
Get in touch with SOCOTEC's Water Treatment & Equipment team to discuss your individual requirements.
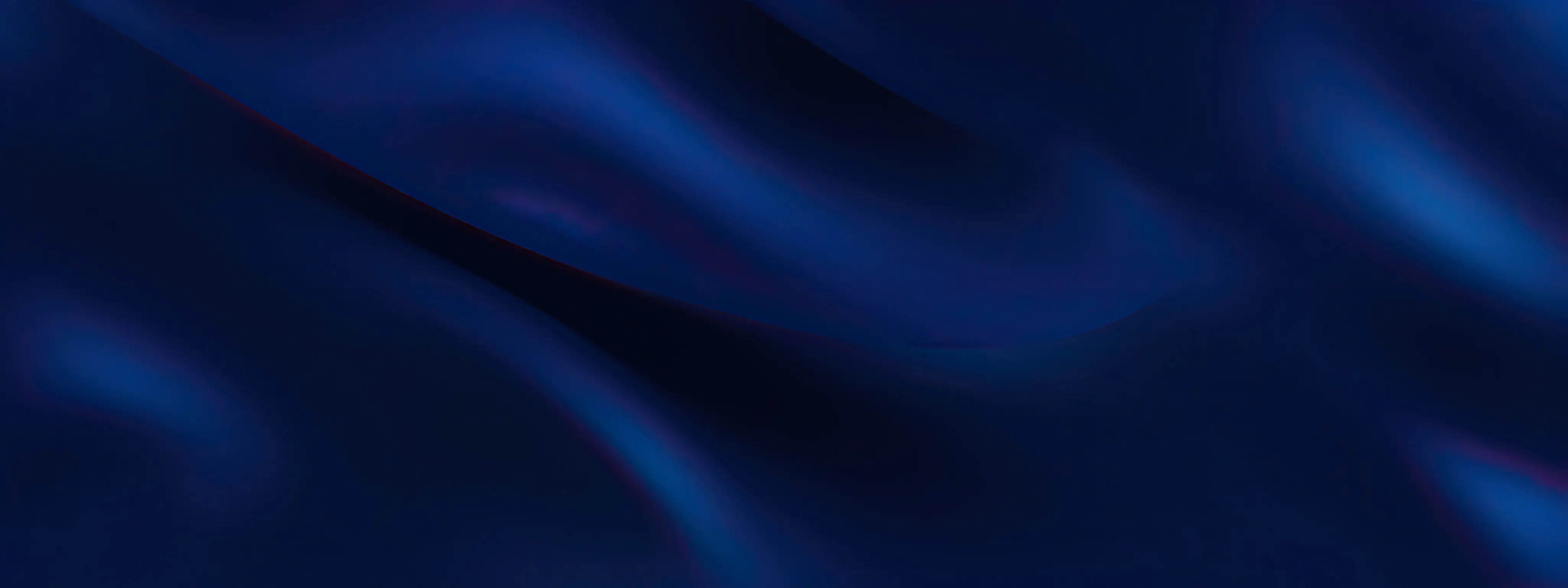
You might also like
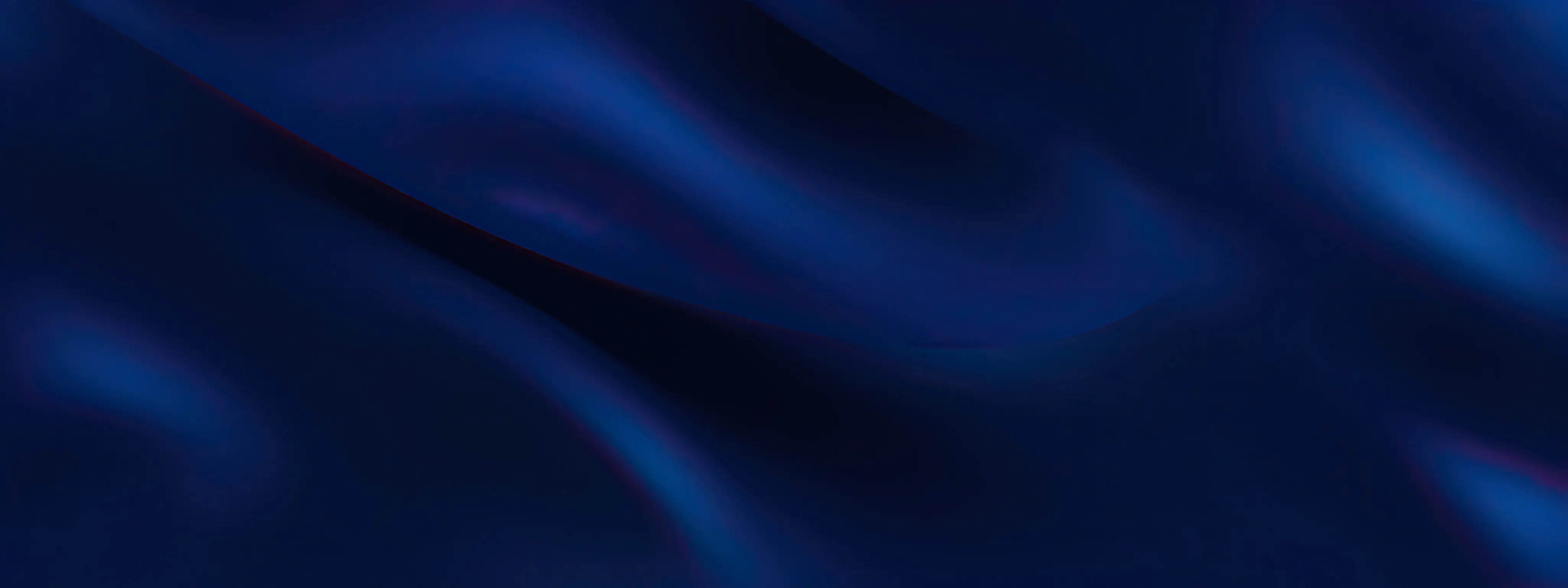
Add new comment