From cleaning train exteriors/shed inspection pits to filling toilet tanks on carriages, water fulfils a host of different functions in order to keep the rail industry operating. Once used, water is almost always returned to the environment in the form of effluent discharges and waste, either to the foul sewer system managed by the local water utility company or to controlled sources such as rivers and streams.
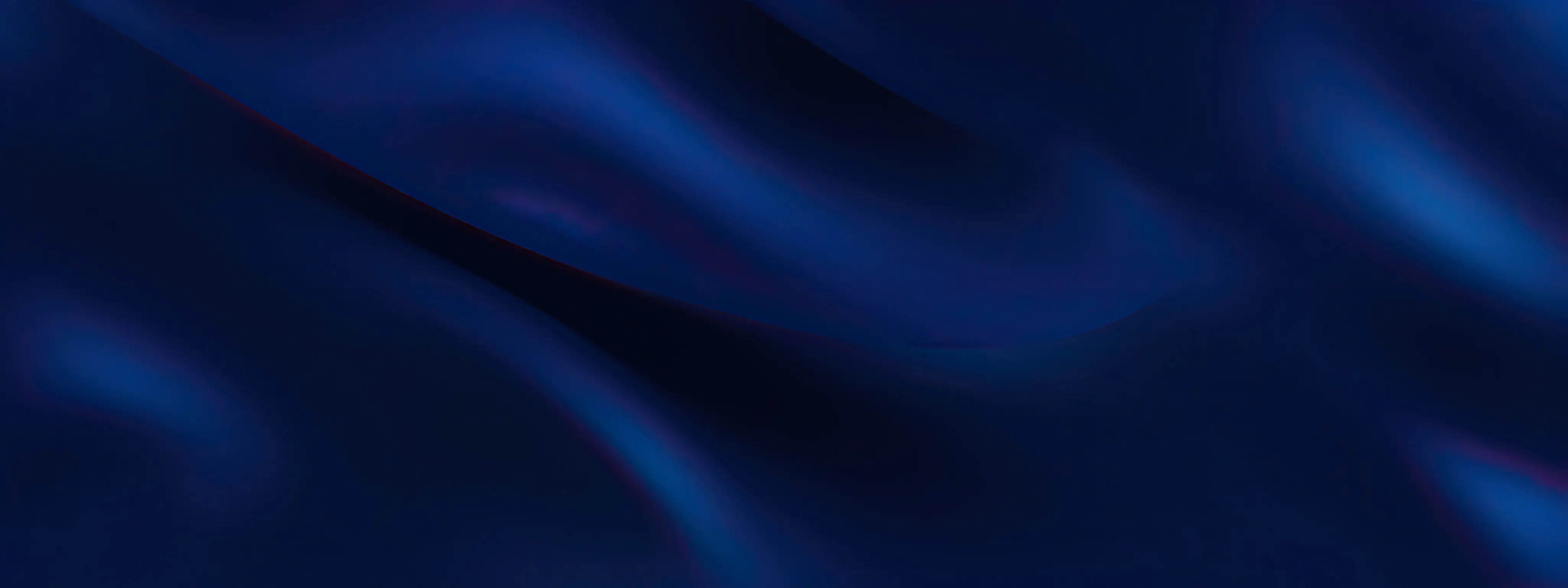
Trade effluent and wastewater discharge can be a costly necessity which, if not monitored and managed correctly, can have a detrimental impact on the environment, as well as having severe legal and financial implications. But how can organisations remain compliant when it comes to managing the quantity and quality of effluent produced by railway traction and at rolling stock maintenance depots?
What is effluent and where can it be found on the railway?
Effluent is any liquid waste that arises from domestic or industrial purposes that is discharged from a particular source and released into the environment. It can be separated into three categories – domestic effluent, trade effluent and surface drainage. The most common form produced within the rail industry is trade effluent, which arises from industrial and commercial activities, such as train maintenance and cleaning activities.
Effluent is created at every railway maintenance depot, and while its quality and quantity may differ, wastewater and discharge is commonly generated by a number of methods:
- Leakages and seepages can occur from both stabled rolling stock and depot facilities such as refuelling systems. Contaminants such as diesel fuel and lubricant oil from engines can leach into the track ballast and potentially contaminate track drainage systems, while leakages from storage tanks, supply pipework and pumps can lead to contamination of nearby drainage systems
- Small quantities of diesel fuel/engine oil and coolant can be spilled during the routine servicing and maintenance of rolling stock. This can contaminate the surrounding area, usually in areas of the depot such as inspection pits and fuelling aprons. The waste from maintenance and servicing activities contributes to the majority of pollutants found in effluents at rail depots, including diesel fuel oil, engine lubricant oil, hydrostatic and gearbox oils and detergent-based cleaners
- Surface water arising from rainfall runoff originates in access roadways, car parks, areas of hardstanding and track drainage. Surface water drains are prone to contamination from accidental spillages, leakage and historical contamination
- Exterior cleaning of rolling stock, together with the cleaning of shed floors and depot inspection pits to remove the build-up of dirt, oil and grease can give rise to considerable quantities of effluent, with several cubic metres of aqueous effluent generated each day. Various detergents are used depending on the type of dirt requiring removal, and some of the cleaning chemicals can be hazardous to the environment if spilled or stored incorrectly, or if they are not used at the correct strength.
Are there any legal implications surrounding the management of effluent?
Managing environmental pollution and consenting discharges to controlled water is a legal requirement, as well as being part of an organisation’s corporate social responsibility. Businesses in England and Wales must comply with a range of legislation restricting the amount of effluent that is released into sewers or water courses, including the Water Resources Act (1991), Water Industries Act (1991) and Environment Act (1995). Companies in Scotland meanwhile, must comply with Section 26 of the Sewerage (Scotland) Act 2002 and Water Resources (Scotland) Act 2013.
Discharges of trade effluent to foul sewer systems are subject to consents issued by the local water utility company, while discharges to controlled waters such as streams and rivers are subject to permits issued by the applicable environmental agency. Any organisations found responsible for causing pollution or discharging effluent without the consent of the applicable environmental agency or their local water utility company face substantial fines and prosecution, causing negative publicity for the business.
Consent limits restrict the daily volume and maximum discharge rates for effluents, while also setting quality thresholds for a range of chemical parameters. Any effluent released from depots must meet these quality standards, and failure to comply with specified limits – such as pH, suspended solids, oil content and Chemical Oxygen Demand – is considered a legal offence. It is therefore vital that rail organisations have all of the correct consent documents in place for all of their sites to ensure legal compliance.
How can effluent be effectively managed so as not to cause environmental harm?
Rail organisations must identify the on-site activities that take place at their depot that could contaminate drainage systems with effluent, while also understanding the full extent of the environmental risks posed by these activities. Having the appropriate management procedures in place can help to prevent contaminants from entering drains, as well as reassuring organisations that they are adhering to the appropriate legal constraints and minimising environmental harm.
Preventing oil and other contaminants from entering susceptible drainage systems is the first stage of risk management. Site risk assessments can be carried out to identify activities that can affect effluent quality and identify potential Source – Pathway – Receptor scenarios. Different drainage systems on site should be mapped and their layout understood, with gully drains, collection sumps, inspection chambers and manholes clearly identified and correctly colour coded to reflect their status. Collection trays and absorbent materials are commonly used within the rail sector, catching spillages at the source and minimising the risk of contaminants entering drainage systems.
Prior to discharge off site, the majority of effluent discharges from railway sites require some form of treatment. These can range from simple settlement chambers to remove solid material to complex multi-chambered interceptor systems to remove free oil. In some cases, additional chemical/physical treatment may be required depending on the nature of the contaminants present.
Monitoring programmes should be implemented to ensure that effluent discharges to the foul sewer meet the required terms of consent to discharge, or in the case of unconsented discharges to controlled waters such as clean run-off water, that no unexpected contamination is present. The findings of such monitoring programmes in addition to highlighting non-compliance also allows for remedial action to be taken before a major incident can occur.
It is also essential that all staff carrying out activities where effluent is generated are adequately trained to respond to all possible effluent scenarios on site, making sure they are aware of the consent guidelines in order to remain fully compliant.
How can interceptors effectively treat trade effluent within the rail sector?
Interceptors (also known as separators) can be used to ensure that certain contaminants are removed from effluent flows prior to discharge. Nearly all railway maintenance depots that produce effluent will have one or more interceptors on site depending on the amount of discharge generated and the activities being carried out. Types of interceptor commonly found on railway sites include:
- Single or interconnected multi-chamber interceptors (the simplest type of interceptor in use at railway depots, usually located underground or above ground in the form a steel tank)
- Class 1 and Class 2 Klargester/SPEL ‘packaged plant’ type interceptors (usually buried underground/occasionally above ground in mounted frames)
- Titled Plate Interceptors for pumped effluent flows (usually situated above ground)
- Settlement chambers (usually for the treatment of wash plant effluent).
The majority of the interceptors used within the rail industry should reduce certain contaminants by allowing free oil and solids to separate out from the water as the effluent passes through the interceptor. They work by allowing water to flow through the interceptor, while free oil and suspended solids are retained within the individual chambers. It is important that interceptors are subjected to a regular maintenance regime, helping to ensure that the final quality of the effluent obtained from the outlet sampling point is visibly free from oil and has no visible solids content.
How can SOCOTEC help?
SOCOTEC provides a host of environmental monitoring services to ensure that your business maintains full legal compliance when it comes to trade effluent or surface water discharges. For further information on how our professional environmental consultants can support your organisation with environmental compliance and industrial effluent monitoring, click here or get in touch.
Want to find out more about SOCOTEC's services?
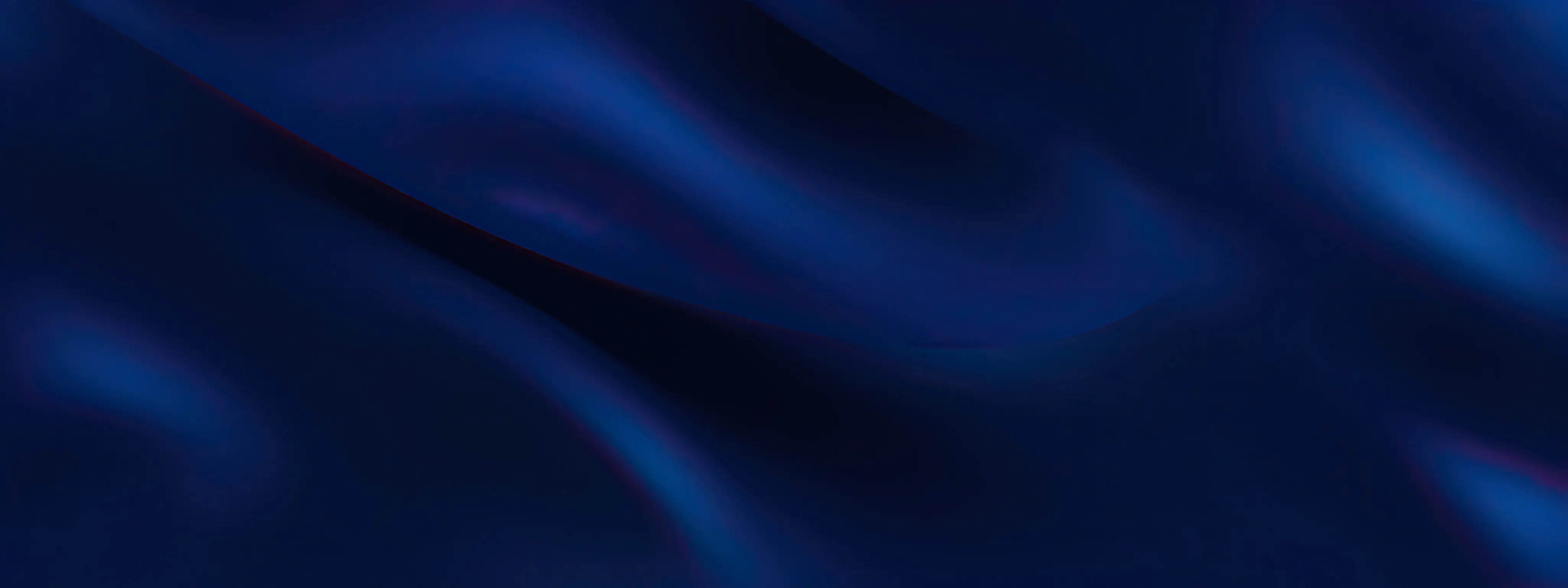
You might also like
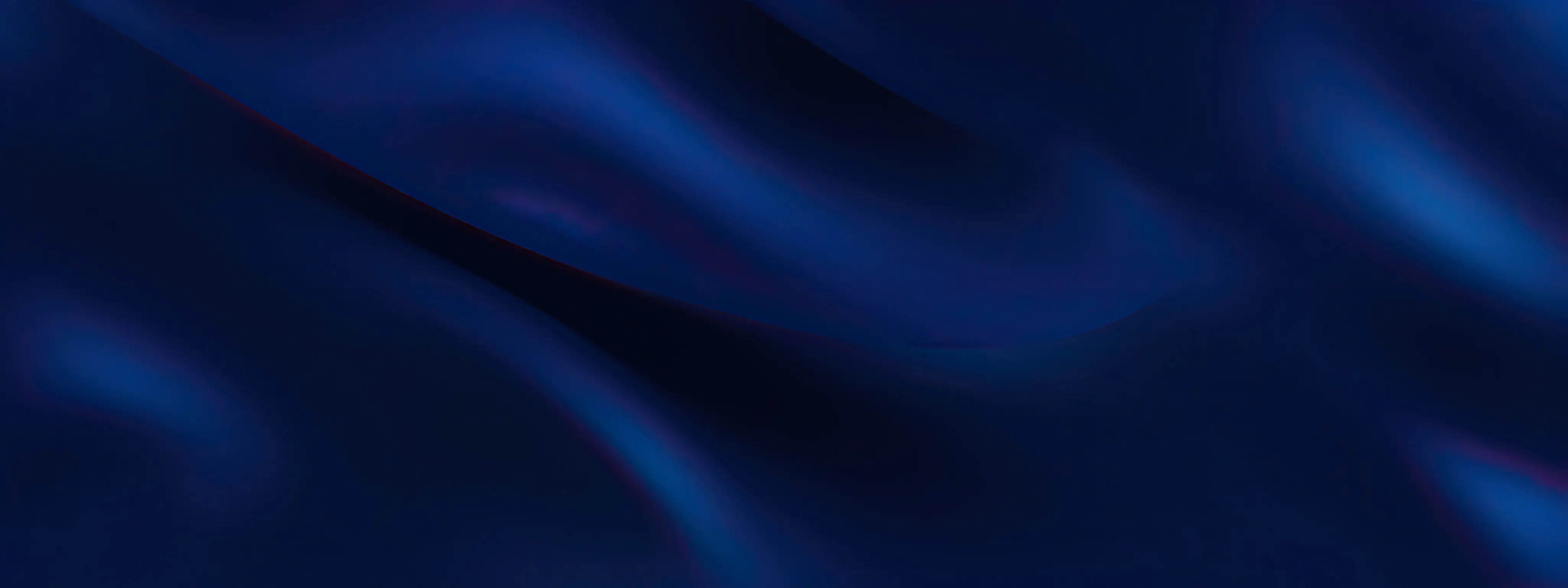
Add new comment