Summary of Works
Client: Port of Dover
Project name: Northampton Quay Wall
Designer: Atkins
Crane Hire: Thanet Crane Hire
Water Weights: Unique Seaflex Ltd (UK).
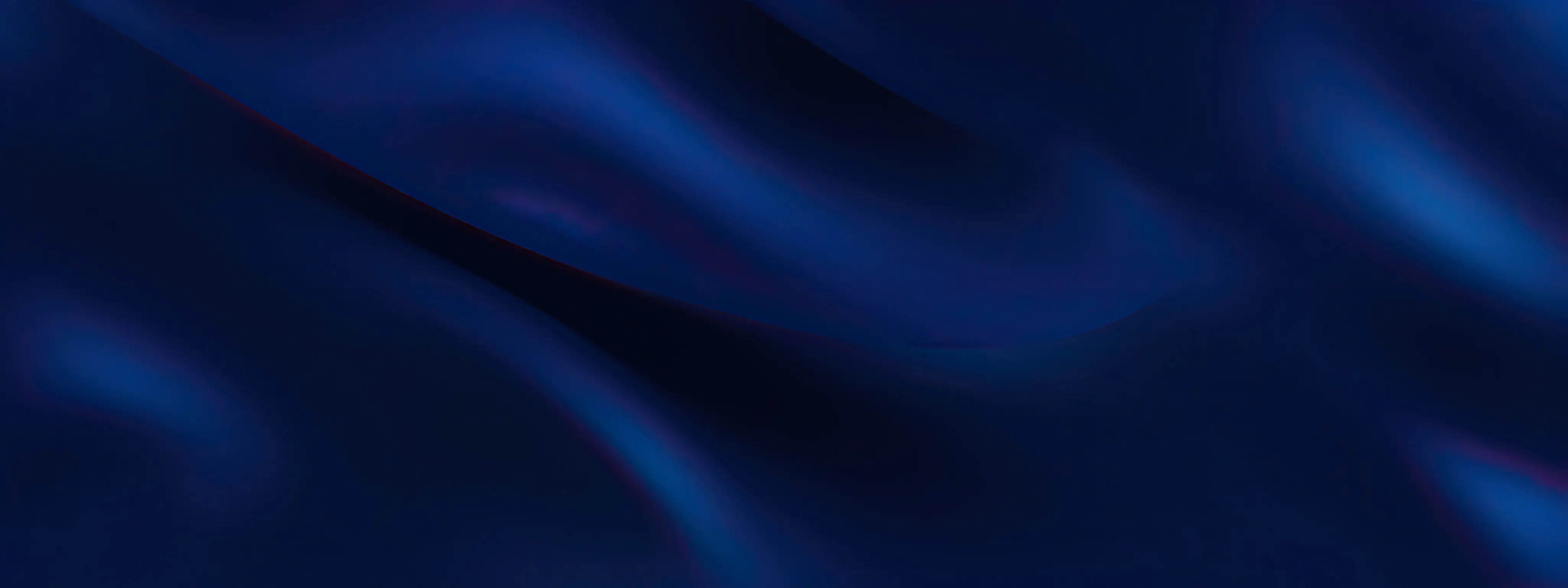
Case Study
Project details
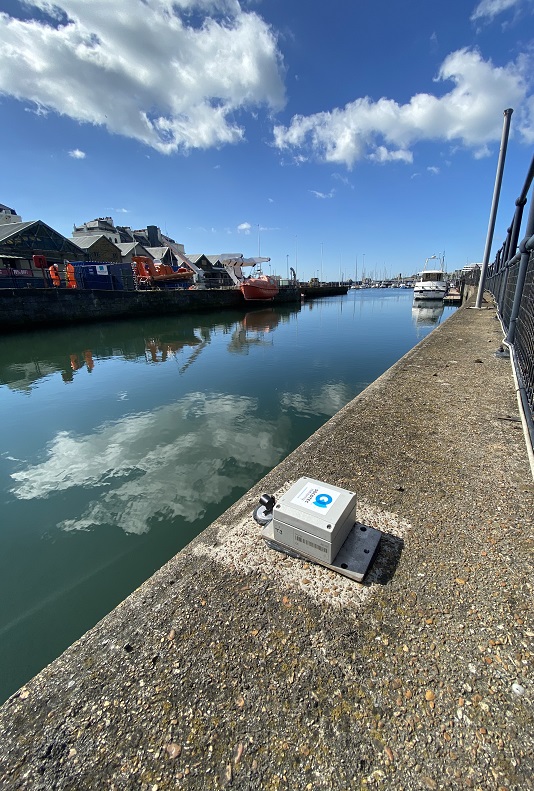
Dover Western Docks Revival (DWDR) is an ambitious £250m project that includes the transformation of the Dover waterfront with a new marina pier and curve, providing the opportunity to attract a host of shops, bars cafes and restaurants. The new marina development includes finger berths for boats up to 18-metres, fuel berth facilities, a new boatyard and boat hoist.
It is this latter item for which the Port of Dover sought SOCOTEC Monitoring’s assistance. Dover’s development plan for the Wellington Dock marina included the design of a mobile boat hoist with a maximum future lift capacity of 75 tonnes. The hoist will operate from an area that is retained by a Grade II listed harbour wall, and the task was to confirm that the structure would remain stable during the operation of the proposed hoist.
Historically, the quayside had been used for commercial operations, such as the loading and unloading of building materials, while part of the area had been occupied by rail infrastructure. With its past land use in mind, it was considered likely that the harbour wall would be capable of supporting the imposed loads from the new crane. However, this assumption needed to be proven.
Dover Western Docks Revival (DWDR) is an ambitious £250m project that includes the transformation of the Dover waterfront with a new marina pier and curve, providing the opportunity to attract a host of shops, bars cafes and restaurants. The new marina development includes finger berths for boats up to 18-metres, fuel berth facilities, a new boatyard and boat hoist.
It is this latter item for which the Port of Dover sought SOCOTEC Monitoring’s assistance. Dover’s development plan for the Wellington Dock marina included the design of a mobile boat hoist with a maximum future lift capacity of 75 tonnes. The hoist will operate from an area that is retained by a Grade II listed harbour wall, and the task was to confirm that the structure would remain stable during the operation of the proposed hoist.
Historically, the quayside had been used for commercial operations, such as the loading and unloading of building materials, while part of the area had been occupied by rail infrastructure. With its past land use in mind, it was considered likely that the harbour wall would be capable of supporting the imposed loads from the new crane. However, this assumption needed to be proven.
A detailed structural analysis was undertaken by Atkins to assess if, as expected, the wall would support the new loads. A ground investigation was also carried out by others to provide Atkins with the necessary ground and laboratory data. This initial investigation and assessment identified highly variable ground conditions which made an analysis of the whole length of quay difficult. The lack of certainty was likely to result in an onerous and costly foundation solution for the new development or the implementation of very onerous operating restrictions, both of which Dover wanted to avoid. The designer therefore suggested that a series of plate load tests be undertaken to supplement the analysis and demonstrate that the wall could safely accommodate the proposed loading.
The challenge
Standard load testing requires defined loads to be applied and a measurement of the settlement to be undertaken. However, the Northampton Quay Wall site had a number of constraints that prevented conventional testing from being deployed. Firstly, access was restricted, and SOCOTEC Monitoring was not permitted to impose any load within two metres of the harbour wall. Secondly, SOCOTEC Monitoring could not apply a pressure greater than 20kPa within six metres of that exclusion zone. The limited and variable depth of the harbour water, as well as existing marine traffic, further restricted access and test options.
Normally in such situations, static loads are directly placed or hydraulically loaded via a 20tonne 360o excavator or similar. However, on this occasion, those conventional options were not possible. Alternative kentledge options were considered, including bespoke frames to transfer the loads and the use of alternative earthmoving plant and trailers. Other kentledge options, such as precast concrete blocks, were rejected because of the safety constraints.
The main challenge was that several plate load tests (the 750mm diameter plate test) had to be undertaken as close to the harbour wall as possible (i.e. within two metres). However, conventional kentledge solutions very quickly exceeded the safety criteria. Furthermore, and due to the listed status of the wall, extremely accurate and near real-time ground settlement and wall deflection monitoring was also required prior to, during and after the testing.
The solution
After much discussion and collaboration between SOCOTEC Monitoring, Atkins, Port of Dover and specialist contractors, Thanet Crane Hire and Unique Group, an ingenious solution was found. The end solution incorporated marine and civil engineering disciplines and leveraged the strengths of SOCOTEC’s combined group capabilities.
Specialist open-top floor test bags that are frequently used in the marine sector were provided by Unique Group to allow uniformly distributed load (UDL) tests to be undertaken. The test bags were filled with 36,000 litres of seawater (36 tonnes) and placed in the six-metre exclusion zone to check that those loads were acceptable. A one hundred tonne crane was then brought to site and carefully loaded and positioned so as not to contravene any of the restrictions. Thanet Crane Hire had designed a bespoke configuration that ensured that three of the four crane’s outriggers would not exceed 20 kPa. This enabled the remaining outrigger to safely apply incremental loads for the 750mm diameter point load test, up to a maximum pressure of 565 kPa.
A layered approach to monitoring
SOCOTEC’s Materials Testing team undertook each plate load test in accordance with a UKAS-accredited test method. However, to ensure that their technician was not beneath the lift area, all measurements of the applied loads and ground settlement were remotely captured using WiFi-enabled equipment. SOCOTEC Monitoring’s survey team also observed survey targets and prisms on the harbour wall while the load tests were undertaken, and wireless biaxial tilt sensors were used to accurately measure rotational movement. Finally, monitoring of the applied loads and movement was provided by Thanet Crane’s on-board computers. Movement trigger limits were defined by Atkins so that in the event of any excessive movement, the testing could be immediately and safely halted.
In addition to the monitoring during the load testing, SOCOTEC’s survey targets and tilt sensors enabled baseline data to be gathered prior to the loads being applied and continued to monitor movement of the existing dock wall after the testing had been completed. The wireless sensors will also assist during the construction phase and with the ongoing monitoring of the listed structure.
“While this project has been one of the more challenging assignments we have undertaken, it was delivered successfully due to Port of Dover and Atkins involving us in the early stages of design, as well as the close co-ordination between all parties involved,” said Stuart Fawcett, senior business development manager, SOCOTEC Monitoring. “It was a real team effort culminating in an exciting and innovative solution that demonstrated what can be achieved with a bit of creative thinking.”
Safety is always paramount
The monitoring and testing were undertaken at height, adjacent to water and with public access in close proximity. Accordingly, safety was of paramount consideration. With many different parties involved, coordination and communication during the operation was also vital. All teams were provided with a detailed overview of the objectives, risks and control measures at the beginning of each shift and all teams communicated via one radio system. As an example of the precautions taken, the crane was positioned in such a way that if the harbour wall did become unstable or even collapse, this wouldn’t lead to the destabilisation of the crane.
“We were very pleased with the end result. Despite all of the restrictions the team had to operate within, the project was able to be completed safely and with minimal disruption to the marina and its users,” said Steve Rawlings, project manager at Port of Dover. “The most satisfying aspect was that it provided us with the comprehensive reassurance we required to progress with the project.”