The storage and use of chemical products is a key feature in many day-to-day railway activities.
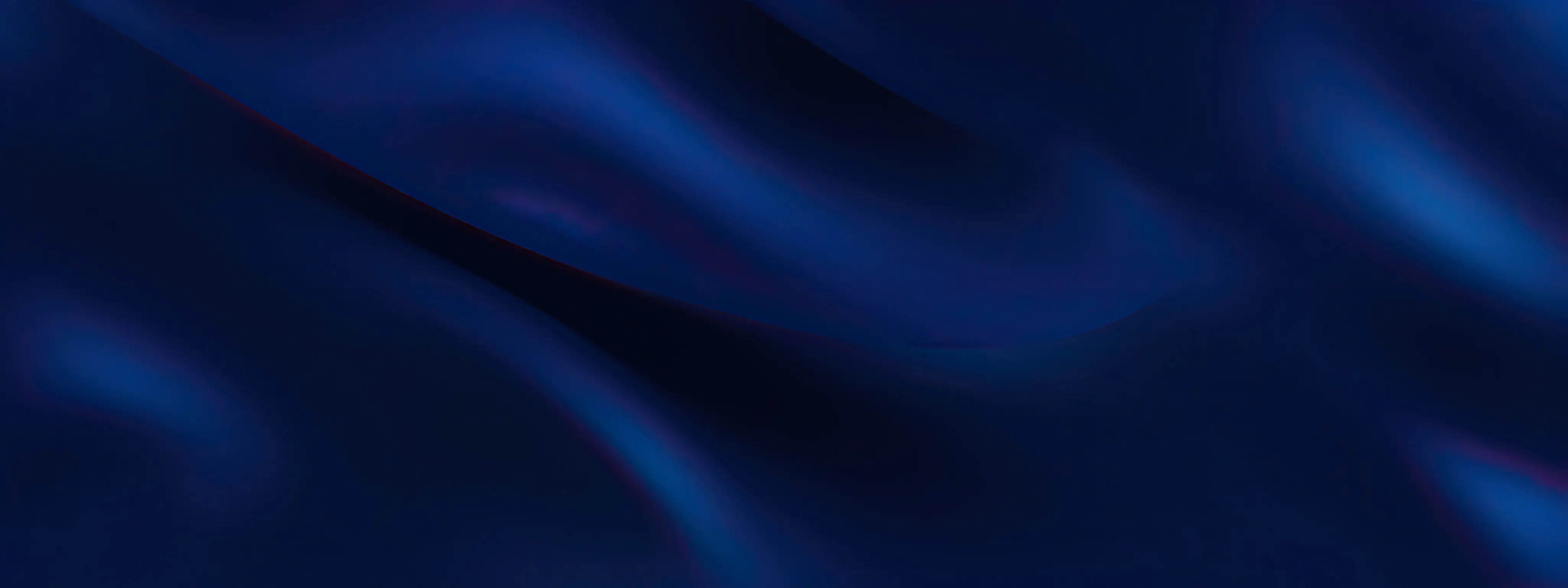
Even in common and well known forms such as cleaning agents, pesticides, lubricants, paints and solvents, the storing of chemicals in some capacity is highly likely. As part of a business’ duty to protect employees, there must be procedures in place for correctly using chemicals.
The Control of Substances Hazardous to Health (COSHH) Regulations 2002 includes guidance on many substances in varying forms, including chemicals. As part of a business’ duty to protect employees, there must be procedures in place for correctly using chemicals. This includes having appropriate risk assessments in place, control measures, training and emergency procedures – see our summative guide.
The purpose of the COSHH regs is to protect the health and well-being of employees, which is required by law. In addition to the COSHH regulations, there are a number of other regulatory obligations when storing and using chemicals that must be adhered to for safe management.
Classifying, Labelling and Packaging Chemicals
When used and stored correctly, chemicals should not cause any harm to humans or the environment – which is why it is fundamental that chemicals are classified, labelled and packaged correctly.
The CLP Regulation refers to the Classification, Labelling and Packaging (CLP) of Substances and Mixtures. Classifying the substance or chemical doesn’t restrict use, but is part of the procedures taken for safe and effective management, handling and use of chemicals. Once classified, they should also follow correct labelling procedures in line with the United Nations’ Globally Harmonised System (GHS) using internationally recognised pictograms.
Safety Data Sheets
Safety Data Sheets (SDSs) are required for all chemical products regardless of whether they are hazardous or not. Safety data sheets have been made an integral part of the REACH system of Regulation. The original requirements of REACH for SDSs have been further adapted to take into account the rules for safety data sheets of the Global Harmonised System (GHS) and the implementation of other elements of the GHS into EU legislation that were introduced by CLP Regulations. A SDS does not replace a risk assessment, but the information contained within the SDS can help to risk assess the chemicals and substances. The SDS should also include information on the hazards posed, storage, disposal and transportation instructions. If unsure, checking with the chemical supplier or manufacturer for advice on storage and handling will ensure you are implementing the correct control measures to minimise risk.
Storing Chemicals
With regard to storage, the segregation of chemicals is important to prevent incompatible materials being stored together which could pose a hazardous risk. Examples include storing flammable materials alongside gas cylinders or the storage of bleach based cleaning agents and acidic products together. A full list of recommendations for separation or segregation of different classes of dangerous substances is outlined in the HSG71 guide, Chemical warehousing: The storage of packaged dangerous substances.
Having a chemical inventory is often a requirement by law. When items are correctly classified, labelled and packaged, correct storage will insure that any hazards are strictly controlled. The inventory should be regularly updated and should be relatively easy to maintain. A well maintained inventory ensures the correct quantities of chemicals are kept in the proper manner and that supplies are not kept past their use-by date.
There should also be appropriate measures in place to prevent spills and leaks, as well as ensuring suitable spill-kits and fire extinguishers are readily available for use, in the event of an emergency.
Frequently checking for damaged containers, and repackaging as quickly as possible where necessary, should be part of the control measures implemented. Storing chemicals should also be done in such a way to minimise the risk of damaging containers.
Other storage considerations include:
- Temperature control of storage facilities, warehouses, cabinets etc to ensure chemicals do not freeze or overheat
- Accessibility to storage areas taking into consideration use of forklifts, pallet trucks etc
- Placement and accessibility of Emergency kits
- Avoidance of over-purchasing and excessively storing potentially hazardous chemicals to minimise the hazards/risks posed
Full considerations for chemical storage can be found in the guides:
Chemical warehousing: The storage of packaged dangerous substances HSG71
HSE guide to health and safety for warehousing and storage (HSG76)
The storage of flammable liquids in containers – HSG51
Do you require further guidance and support on safe chemical storage?
Our expert teams are on hand to help your organisation remain fully compliant with chemical legislation.
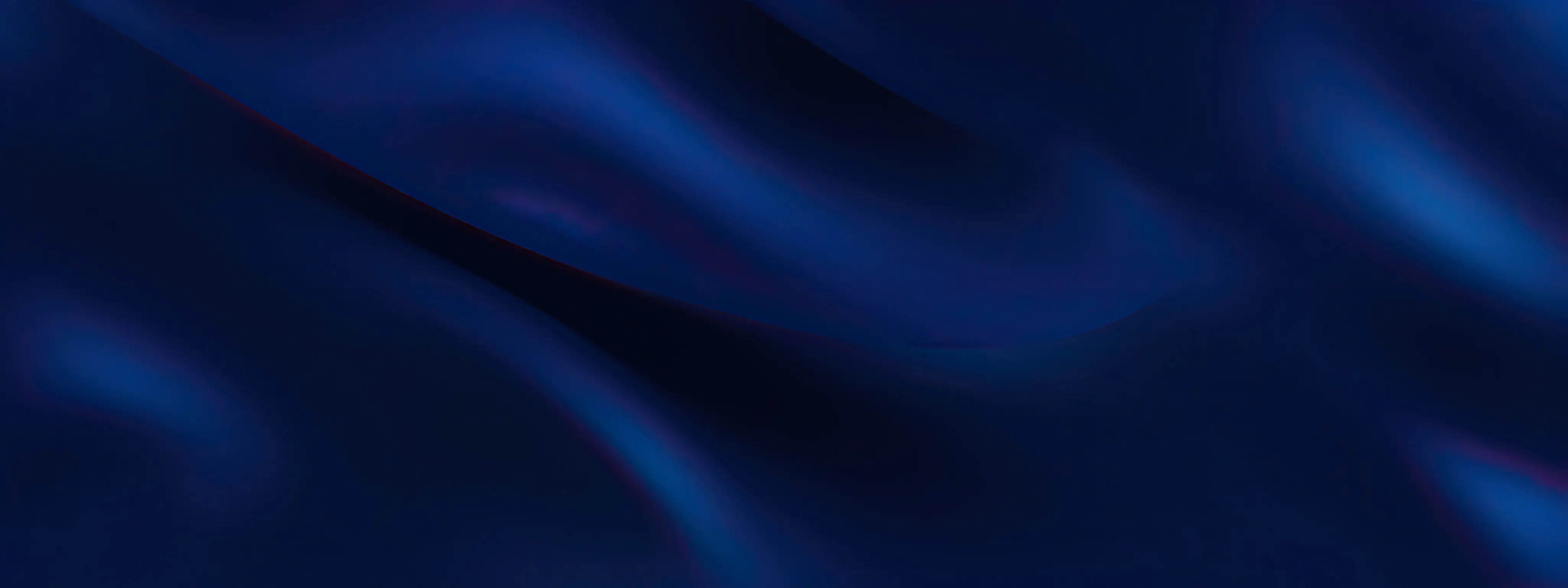
You might also like
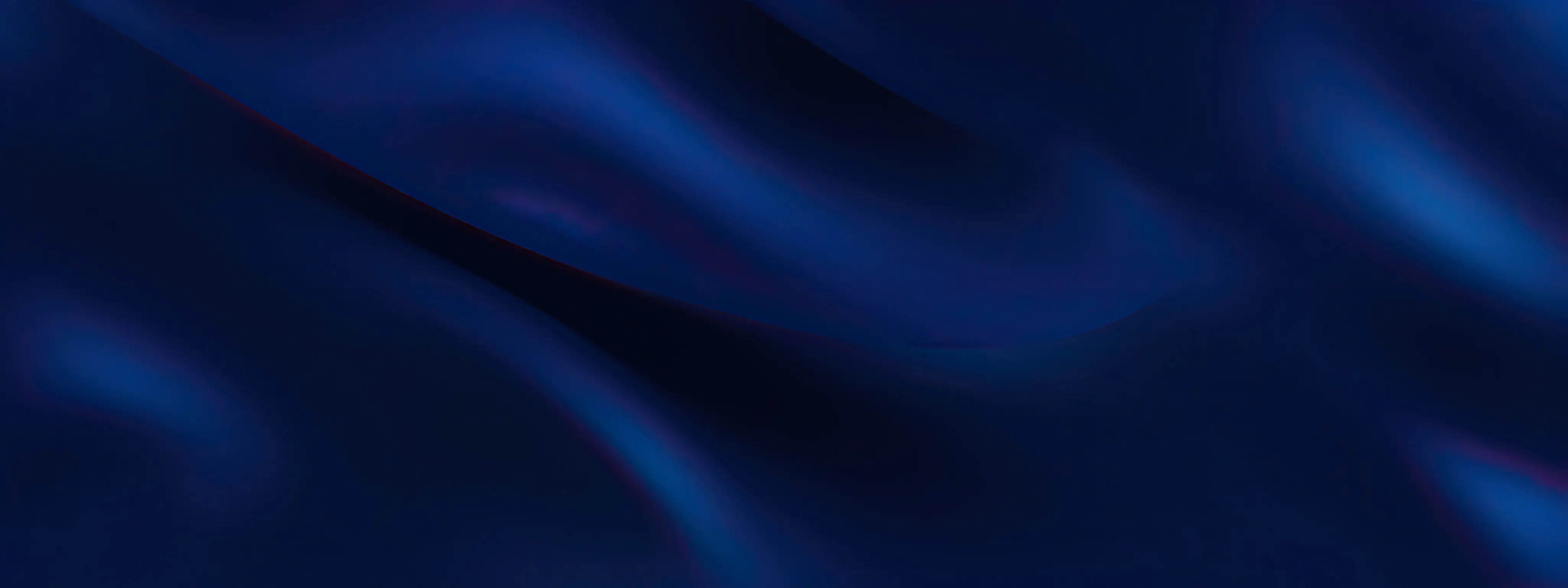
Add new comment