As the demand for railway transportation continues to grow at a rapid pace, maintaining the efficiency, reliability and safety of trains is of paramount importance.
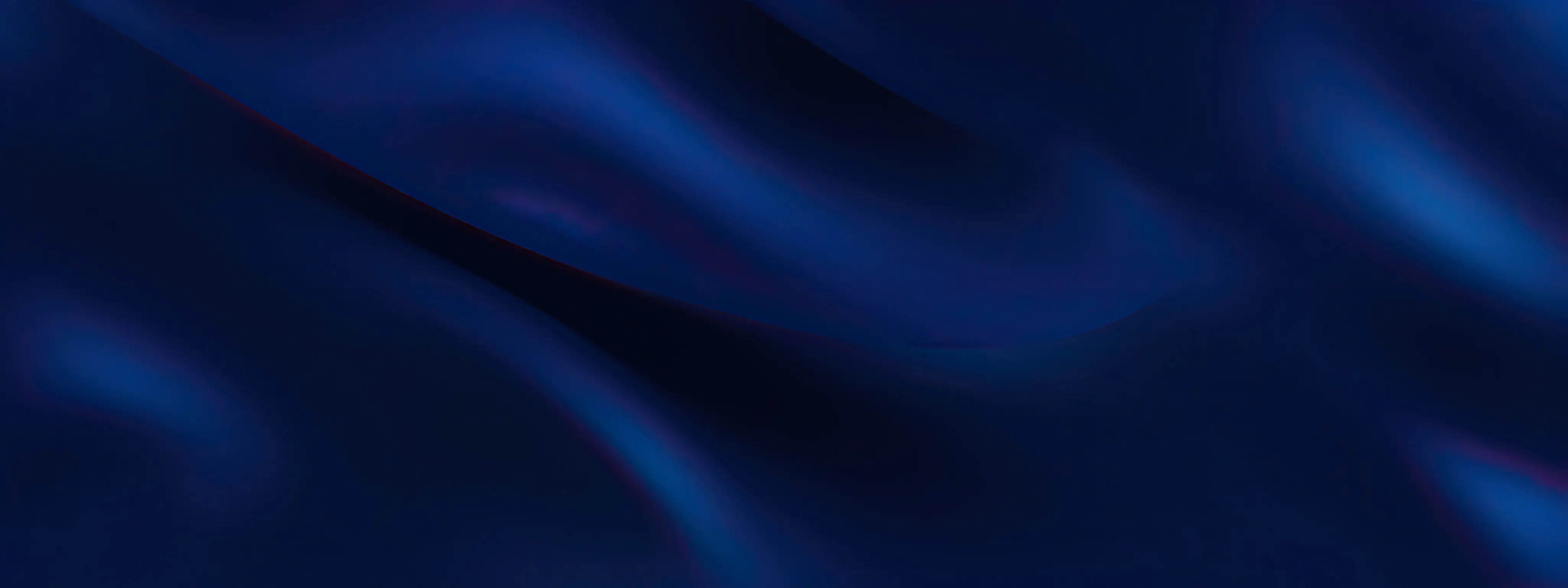
With the potential to cause widespread disruption and delays if asset failure takes place, the testing, monitoring and analysis of the condition of oils, coolants and greases is therefore fundamental to the safety and reliability of locomotives.
The primary function of oil as a lubricant is to reduce surface friction, remove heat, minimise water and control contamination. Oil analysis, therefore, can provide a wealth of information on the long-term performance of assets in relation to these lubricative functions, as well as ensuring that the machinery being tested is operating to its full capacity.
Why is it necessary for oils, coolants and greases within trains to be tested?
In order to minimise disruption on the railway, lubricants need to be monitored regularly to identify that the asset is fit for purpose and operation. For example, if metal particles are detected in the lubricant, this indicates that the asset has been prematurely worn, which, if ignored, can lead to a component failure.
Given the numerous capacity issues affecting the rail sector, including the need for minimal downtime and a smoothly operated service, ensuring that every available unit is in full working order and ready for use is crucial. While the cost of monitoring may seem an unnecessary expense, particularly when railway operations seem to be running smoothly, the benefits of oil monitoring far outweigh the initial spend. When you consider the fines related to train delays and blocked railway lines, extensive equipment repair costs and other such ramifications associated with downtime, paying for regular maintenance is by far the most sensible option. This not only guarantees safety and consistency of the rail system, but also maintains a positive track record when operations function as normal.
Considerable savings can also be made by identifying potential and future problems via the analysis of processes and the asset environment. By determining all of the possible root causes and conditions that could ultimately lead to the breakdown and failure of railway operations, additional preventative and predictive maintenance can take place on the rolling stock. This further ensures the longevity of the locomotive itself by protecting the integrity of the engine and machinery, as well as dramatically reducing downtime if or when the failure does eventually occur.
How does oil condition monitoring work?
To accurately assess the status of the oil and detect any potential early faults, screening tests will monitor such properties as particle size, oxygen content, oil viscosity, total acid number (TAN), total base number (TBN) and total insoluble matter (TIM). By conducting oil condition monitoring at regular intervals, rail operators can be made aware of any recognisable faults that would otherwise go undetected until the asset had failed.
ICP spectroscopy provides a full elemental scan to determine the wear, oil additive and external contaminants. Levels of iron, copper and zinc within the engine oil, transmission or diesel fuel can indicate that the bearing or gears are degrading or wearing down. Likewise, ageing oil can be detected through the levels of viscosity, oxidation and acid present, which indicates that the oil and asset may not be performing at maximum efficiency. Once these results have been obtained, train operators are able to make an informed decision to change the oil, which can ultimately prevent a systematic failure further down the line. Meanwhile, the presence of silicon and sodium indicates the ingress of dust/dirt into the asset. This can lead to further deterioration if neglected, as it highlights that dirt can no longer be prevented from entering and damaging the system.
For engines on rolling stock, there are a number of analysis types that can provide crucial information on the integrity of the component. A basic comparison between new and used oil will determine the extent to which fuel has been diluted; the lower the viscosity of the oil, the more likely it is to generate friction between the surfaces and cause the system to deteriorate.
Take a look at this infographic which provides further insight into the various methodologies that can be used to carry out oil monitoring procedures.
How frequently should oil condition monitoring take place?
Oil condition monitoring can identify a root cause or condition that can lead to failure; identify an early stage fault that might otherwise go undetected; identify the location and cause of failure; determine severity of the condition and potential correction actions needed; and identify the cause of machine failure after the event.
The monitoring frequency (and associated sampling plan) relies on usage of the asset. Infrequently used assets must still be maintained, and time-based sampling is usually the most appropriate programme for oil condition monitoring. Frequently used assets or high mileage trains should be monitored based on mileage use as the inspection should increase. Another consideration for the sampling plan is: how critical is this asset? Where appropriate, it may be beneficial to conduct additional maintenance and monitoring to reflect how important or how intensively used the asset is.
Is oil condition monitoring still effective if asset failure has already taken place?
While preventative and predictive maintenance offers the most benefits to support continuous and efficient rail operations, this is not to say that oil analysis does not provide information at other stages of the maintenance programme. Nevertheless, it should be noted that maintenance managers and engineers should seek guidance from specialists in order to ensure that a thorough investigative fault diagnosis is carried out.
Screening tests can assess the status of the asset for contamination, wear damage, acidity, thickness/age of oil and particle size. These indicators will provide information on where exactly the fault began and whether it could have been avoided.
Reactive analysis – otherwise known as post-mortem analysis – examines the condition of the oil and lubricant following asset failure. However, once at this stage, the rail operator will already be suffering the consequences of having rolling stock or rail equipment out of action as a direct result of potentially costly repairs and delay compensation.
How can SOCOTEC help?
With over 50 years’ experience providing testing and analytical support on the railways, SOCOTEC is best placed to conduct a range of oil analysis measures. Building on the rich heritage of its laboratories and the vast experience of the analytical team, SOCOTEC offers a thorough and proactive oil monitoring programme that combines client focus with the latest in equipment and methodologies, and it is this approach that has allowed us to maintain many of our key client relationships over the years.
Does your rail organisation require support with oil, lubricant and fluid condition testing?
SOCOTEC’s oil, lubricant and fluid testing services extends to both railway and lineside equipment.
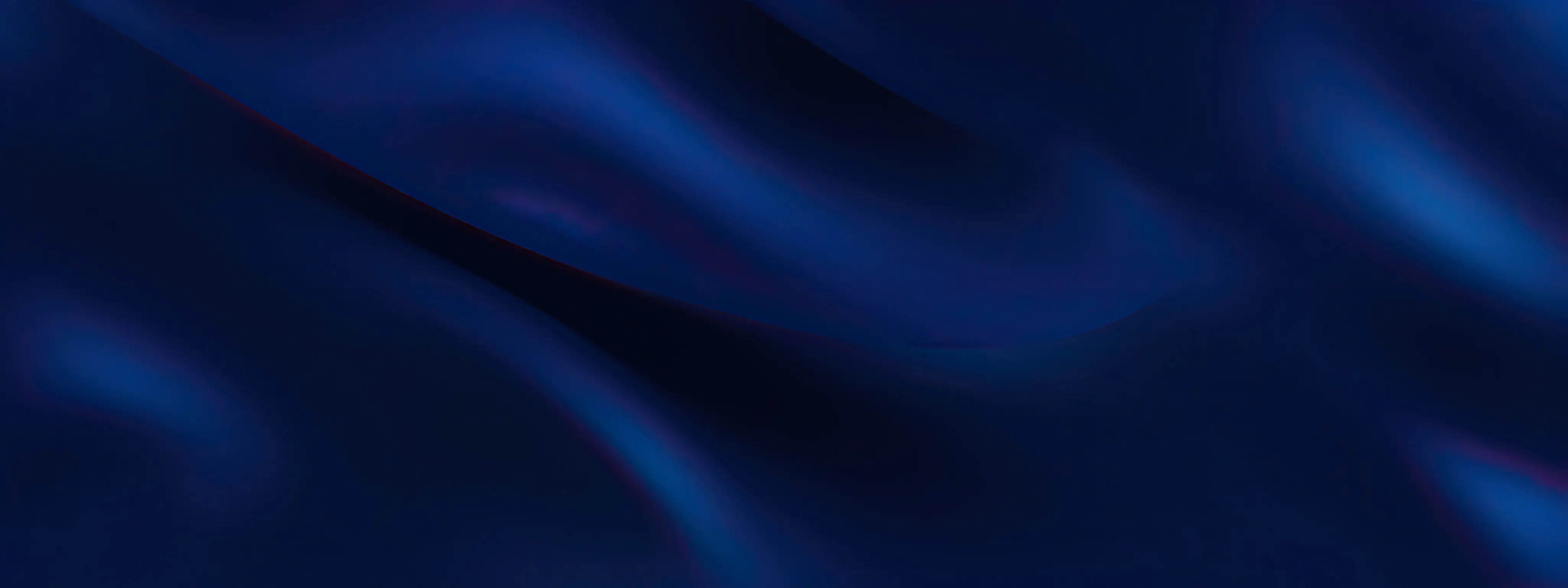
You might also like
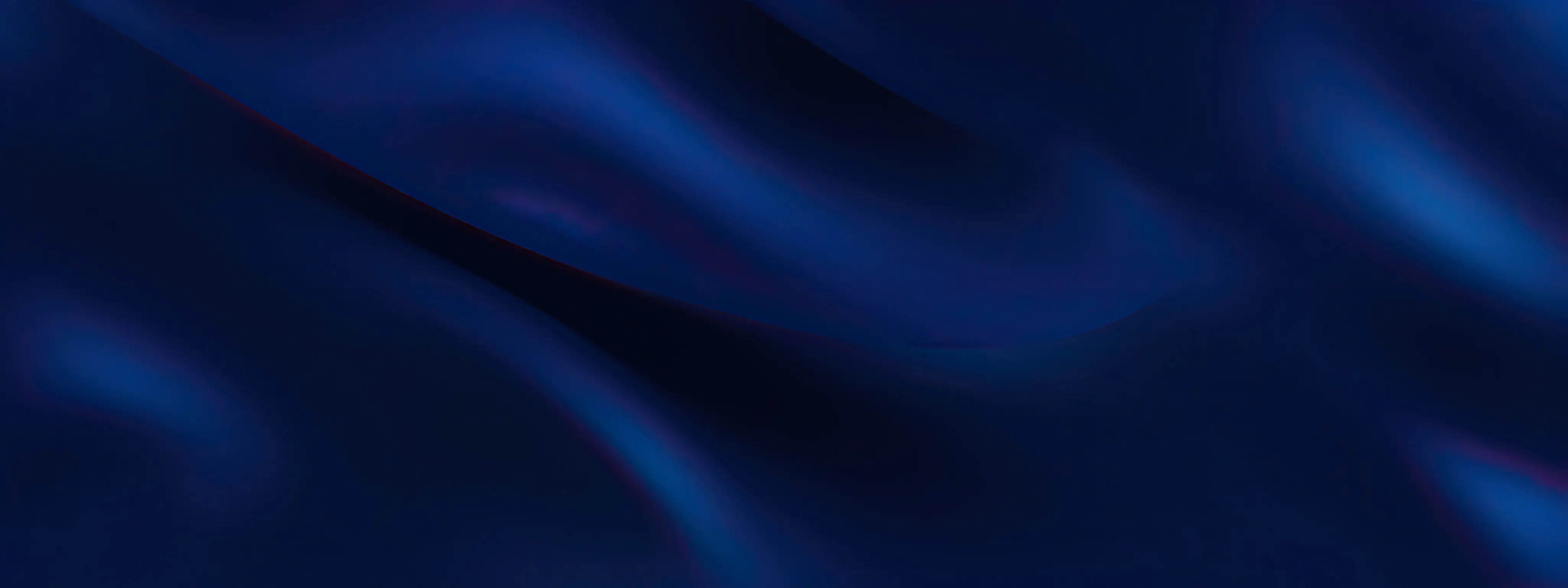
Add new comment