SOCOTEC – the UK’s leading testing, inspection and compliance company - has been working alongside Timothy Taylor’s Brewery to support their brewing process with efficient sanitation methods.
Summary of works
Client – Timothy Taylor's Brewery
Location - Yorkshire
Food & Beverage
In the food and beverage industry, outstanding hygiene standards are paramount for both quality and food safety, as well as ensuring optimum performance of all equipment and processes.
Based in Yorkshire, Timothy Taylor’s is an independent, family-run brewery with 160 years’ experience, using the finest ingredients to brew the best possible beers. Landlord, a brewery favourite, has won more awards than any other beer.
Fermentation vessels are an essential component to any brewery, where the yeast converts the wort (malt extract and water) as it ferments into beer; the fermentation temperature defines a beers’ flavour. A common issue that can occur is the build-up of biofilm within the cooling jackets of the fermentation vessels, and at Taylors some date back to the 1960’s. Biofilms most often consist of many species of bacteria, as well as fungi, algae, protozoa, debris, and corrosion products. Essentially, a biofilm may form on any surface exposed to bacteria and some amount of water. In the food and beverage industry, biofilm often impacts on industrial processes but can also affect the thermal performance of some manufacturing equipment.
Loss of cooling efficiency and the consequential potential impact on product quality in this instance, could have costly implications, so when Timothy Taylor noticed the thermal performance of their cooling jackets deteriorating, they sought support from water equipment specialists and consultancy experts, SOCOTEC. In order to recommend a bespoke solution, SOCOTEC conducted a site survey and liaised directly with the brewers at Timothy Taylor to discuss the requirements of the brewery.
To treat the biofouling of the cooling circuit, SOCOTEC recommended an Ozone unit (OFG-30-01W) with UV (V170) to provide direct chemical-free disinfection and return the cooling circuit to full efficiency.
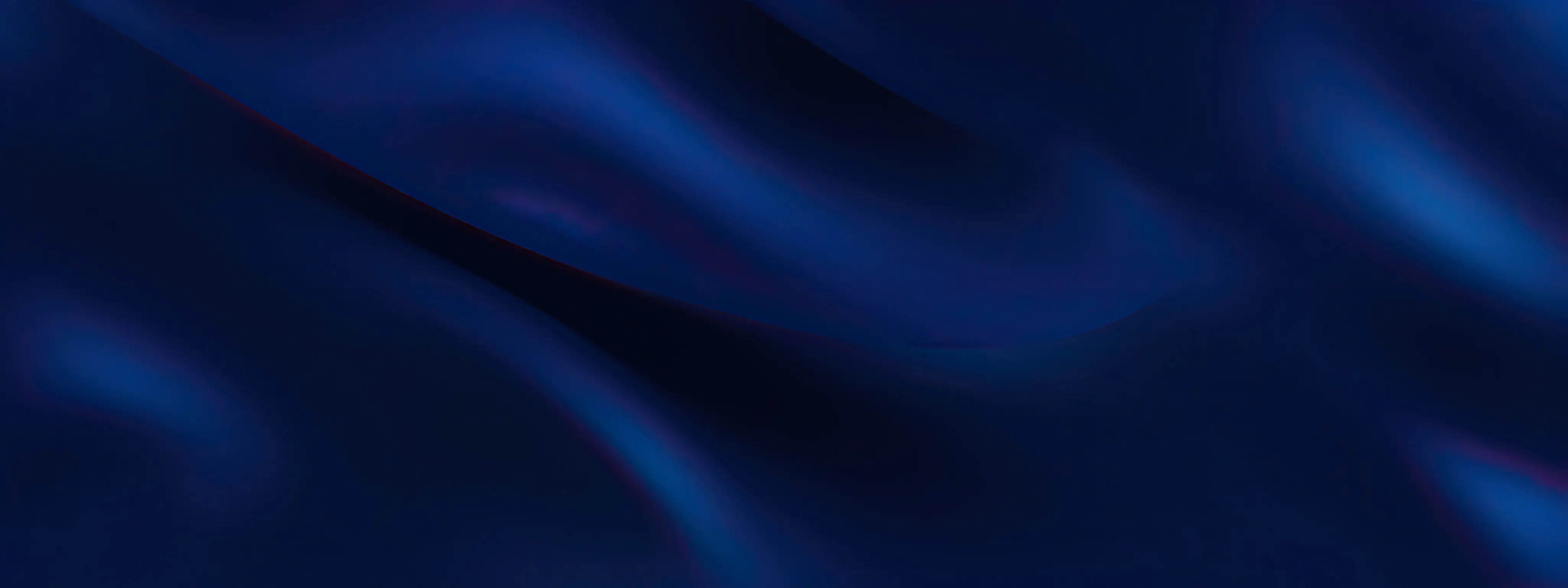
Case Study
Why Ozone?
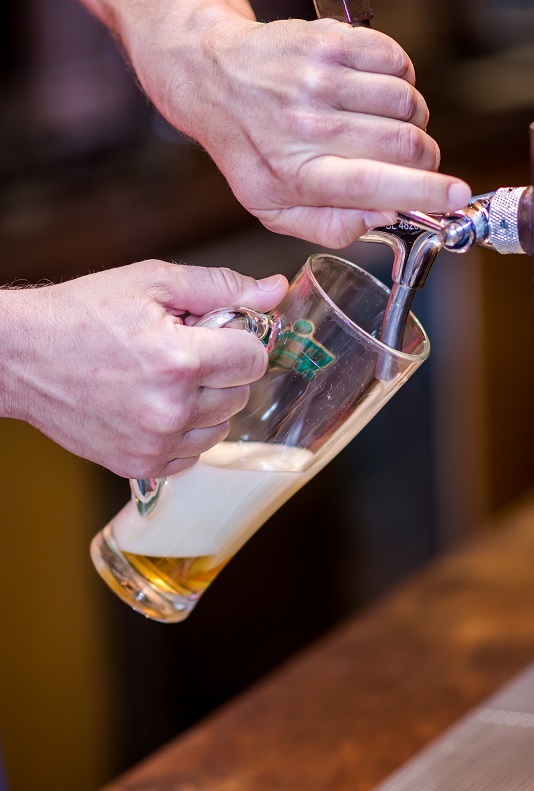
Ozone has been used for over 100 years as a method of disinfection in the brewing industry. It is a powerful oxidising agent produced in-situ, using only oxygen as its raw material.
More frequently, companies are questioning the effects that traditional chemical sanitation methods (such as hypochlorite, peracetic acid (PAA) or hydrogen peroxide) have on their equipment condition, end product, and the environmental impact when waste water is drained.
A proven alternative, Ozone is capable of destroying all bacteria, algae and biofilms with no risk of resistance build up or toxic residue. It removes the need for handling, storing and administrating harmful chemicals while minimising water consumption.
Ozone has been used for over 100 years as a method of disinfection in the brewing industry. It is a powerful oxidising agent produced in-situ, using only oxygen as its raw material.
More frequently, companies are questioning the effects that traditional chemical sanitation methods (such as hypochlorite, peracetic acid (PAA) or hydrogen peroxide) have on their equipment condition, end product, and the environmental impact when waste water is drained.
A proven alternative, Ozone is capable of destroying all bacteria, algae and biofilms with no risk of resistance build up or toxic residue. It removes the need for handling, storing and administrating harmful chemicals while minimising water consumption.
Starting the improvement process
In October 2017, SOCOTEC’s water equipment team commissioned the units on Timothy Taylor’s brewery site in Keighley, keeping production downtime and disruption to a minimum. The UV unit was installed inline as part of the recirculation loop from the collection tank pump outlet.
Installed next to the collection tank and pump set, the Ozone unit – along with Ozone injection pump – was connected to the recirculation loop to deliver variable ozone concentrations to the system in line with flow. To control the Ozone dose level, a dissolved Ozone sensor was also fitted; this enabled accurate and precise ozone levels to be monitored and log the data.
Ozone units can be fitted into many applications. As the collection tank was situated in the humid cellar, the unit also required compressed air for the internal oxygen concentrator.
While the UV unit provides proven disinfection during normal operation, the Ozone unit provides Cleaning in Process (CIP) to remove the build-up of biofilm and deep clean the system, as and when it is required. CIP cleanses the inside of the process equipment, reaching areas where physical cleaning is not possible.
Nick Berkovits, Second Brewer, at Timothy Taylor’s, commented: “It was great to see immediate results from the CIP which lead to dramatic thermal improvements in the months following commissioning.”
As SOCOTEC advised, the system would require more frequent cleaning in the initial stages, but it was promising to see improvements from the Ozone installation instantaneously.
Remote Monitoring
For continuous performance monitoring of the unit, SOCOTEC installed a GSM remote monitoring function. This enables both Timothy Taylor and SOCOTEC to monitor and log the unit’s performance.
To fully integrate the equipment and to make it easier for Timothy Taylor to use on a day-to-day basis, a Programmable Logic Controller (PLC) controls all functions of the Ozone generator, and Ozone injection pump, and the settings for the unit can be adjusted by the cabinet door mounted HMI.
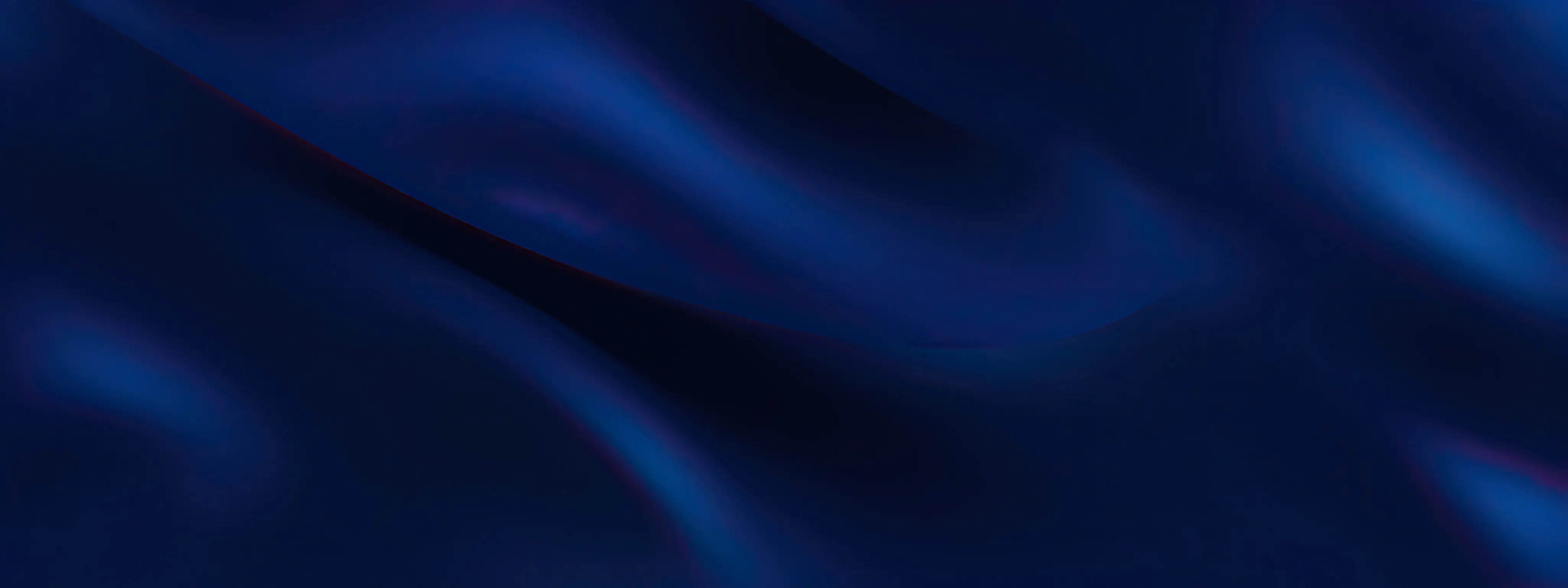
Case Study
Results as expected
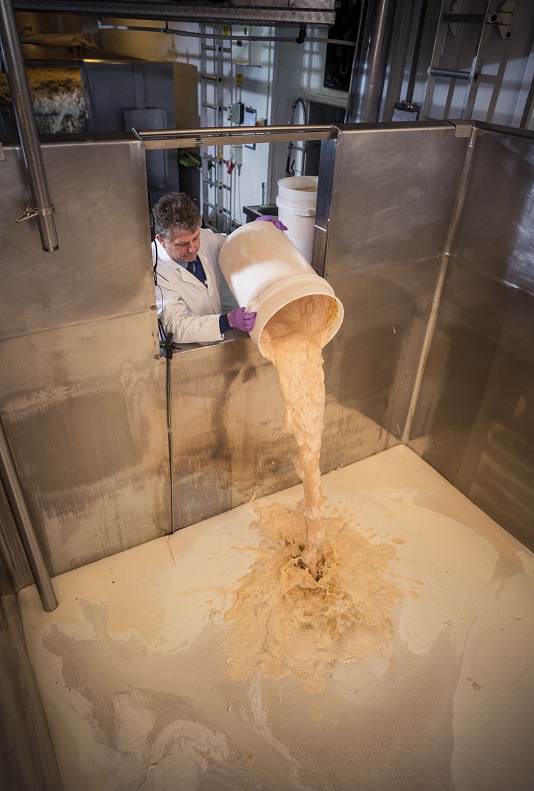
Four months on, Nick further commented: “We’ve been very pleased with the result so far and I am keen to see the ongoing benefits of using both the Ozone and UV units. Cleaning in place has taken place every weekend since the equipment has been installed. This keeps our running costs down as the performance of our cooling jackets has improved. We refuse to compromise on quality at Timothy Taylors Brewery so, with the support of this innovative water treatment, we can continue to brew our beers to the highest standard.”
Grace Williams, technical sales manager, added: “With the food and beverage industry, sanitation and hygiene is one of the most important factors to consider, ensuring a safe product is being produced. For most organisations, sustainability and minimising energy consumption is now a huge focus - especially in this environmental and sustainable age.
Four months on, Nick further commented: “We’ve been very pleased with the result so far and I am keen to see the ongoing benefits of using both the Ozone and UV units. Cleaning in place has taken place every weekend since the equipment has been installed. This keeps our running costs down as the performance of our cooling jackets has improved. We refuse to compromise on quality at Timothy Taylors Brewery so, with the support of this innovative water treatment, we can continue to brew our beers to the highest standard.”
Grace Williams, technical sales manager, added: “With the food and beverage industry, sanitation and hygiene is one of the most important factors to consider, ensuring a safe product is being produced. For most organisations, sustainability and minimising energy consumption is now a huge focus - especially in this environmental and sustainable age.
“By removing biofilm from Timothy Taylor’s cooling jackets, SOCOTEC can support in returning the equipment to optimum thermal performance. We specialise in non-chemical disinfection methods as it has immediate environmental benefits. Also, with total biological control, Ozone is easily monitored, safe and reliable. We are looking forward to an ongoing relationship with Timothy Taylor’s Brewery to meet their continuing needs in the brewery industry.”