SOCOTEC Monitoring – formerly ITM Monitoring – has been contracted by Transport for London to monitor the Network Rail High Speed (NRHS1) tunnels during the construction of the new viaduct, as part of the Barking Riverside extension.
Summary of works
Client - Transport for London
Service - Monitoring and Surveying
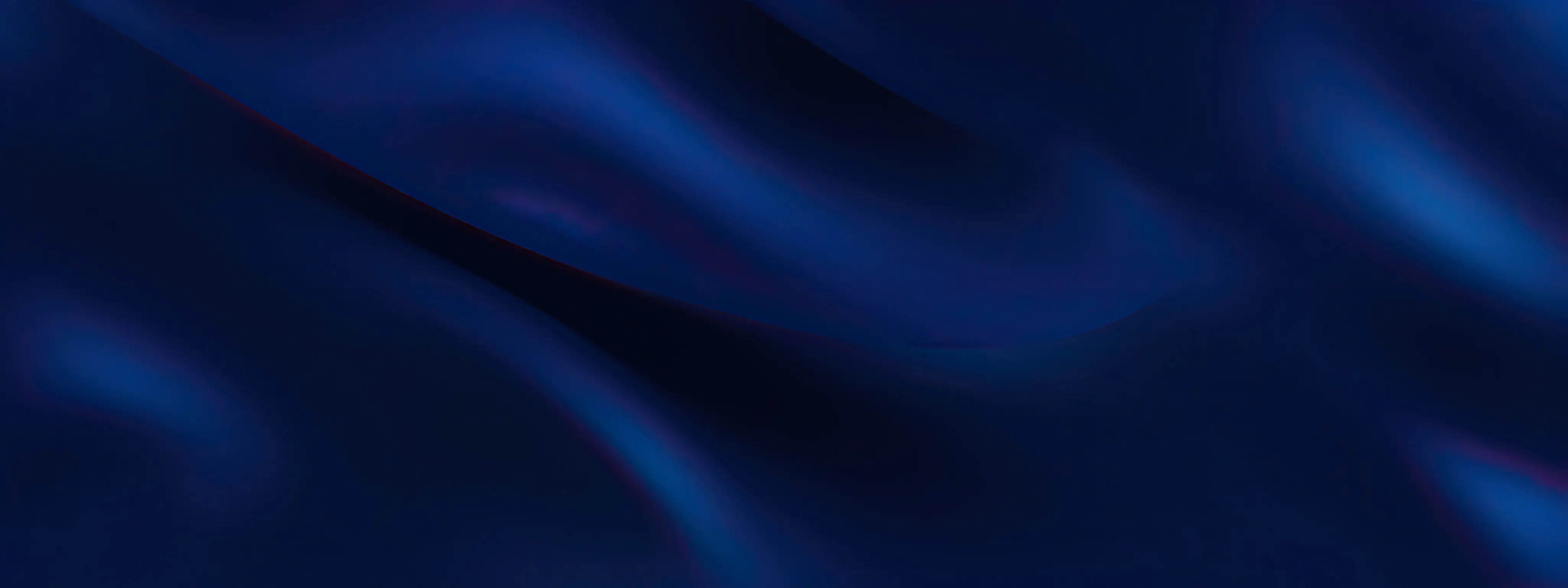
Case Study
Site background
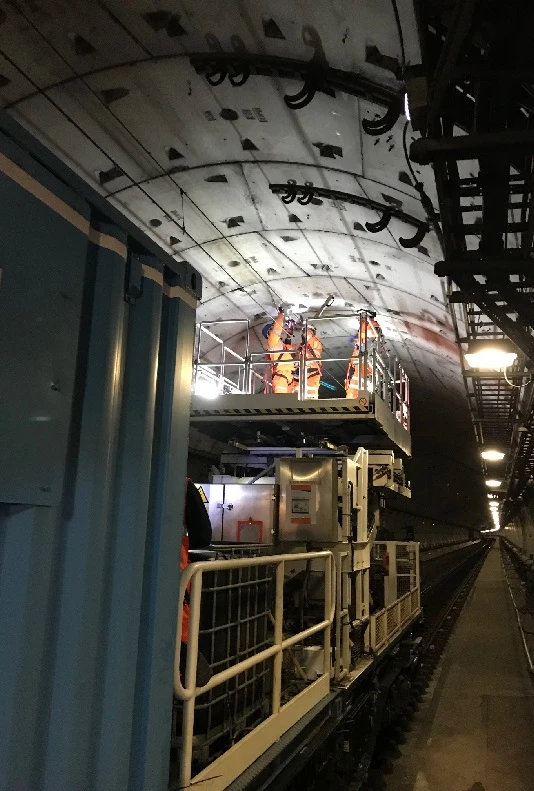
In 2007, planning permission was granted to build 10,800 new homes at the site of the former Barking power station. It is set to provide housing for 29,000 people on the banks of the River Thames and will create a brand new area of London with several leisure and shopping facilities, as well as seven new schools and its own healthcare facilities.
In order to reaffirm this significant housing development as an attractive East London location, a dedicated rail station is being constructed. The new Barking Riverside station will provide easy access to the city by adding 1.5km to the existing Gospel Oak to Barking Overground Line. Along most of its route the extension runs parallel to the CTRL tunnels, eventually diverging and crossing these twin bore tunnels by construction of an elevated viaduct. The development of this viaduct has the potential to generate ground movements during deep piling works.
SOCOTEC Monitoring is carrying out monitoring and surveying works in order to detect and manage any potential effects on the CTRL twin bore tunnels during the construction of the new elevated viaduct.
In 2007, planning permission was granted to build 10,800 new homes at the site of the former Barking power station. It is set to provide housing for 29,000 people on the banks of the River Thames and will create a brand new area of London with several leisure and shopping facilities, as well as seven new schools and its own healthcare facilities.
In order to reaffirm this significant housing development as an attractive East London location, a dedicated rail station is being constructed. The new Barking Riverside station will provide easy access to the city by adding 1.5km to the existing Gospel Oak to Barking Overground Line. Along most of its route the extension runs parallel to the CTRL tunnels, eventually diverging and crossing these twin bore tunnels by construction of an elevated viaduct. The development of this viaduct has the potential to generate ground movements during deep piling works.
SOCOTEC Monitoring is carrying out monitoring and surveying works in order to detect and manage any potential effects on the CTRL twin bore tunnels during the construction of the new elevated viaduct.
Challenges faced
It can be a challenge to plan track works as it needs to be scheduled far in advance, usually six months prior to the actual work commencing. With this project, SOCOTEC Monitoring inherited a pre-planned work schedule, limiting the works to a set number of days with the addition of any further dates being unlikely or compromised by being on others’ booked access. This had to be considered when designing the monitoring system as the implementation needed to fit within the specified time frame.
Under normal circumstances, the monitoring of this kind of asset would require the use of Robotic Total Stations (RTS) and prisms. For this project, however, there were several reasons why this solution would not be suitable. Optical systems rely on the line of sight between each RTS and the prisms it reads. With elevated levels of dust build-up in the HS1 running tunnels, and with passing trains running at high speed (140mph), prism cleaning would need to be undertaken regularly to keep sight lines clear. This would have required further scheduled isolated possessions which are costly and disruptive, and therefore not an option in this case. Additionally, RTS units have the potential to be affected by the speed of the trains and the piston effect of the air they displace, with vibrations impacting the level compensators of the instruments and air turbulence having the ability to cause reading inconsistency.
The monitoring solution
Thanks to the technical expertise and extensive field experience of the engineers at SOCOTEC Monitoring, an alternative solution was devised and implemented. It was decided to use cable free tilt sensors to determine tunnel ovalisation along with cant and twist measurements of the track.
Tilt sensors do not require cleaning, eliminating the need for extensive maintenance and limiting the amount of work and isolation periods required.
As an RTS is connected to a network of prisms, if the instrument fails it means that a large percentage of the system is down in one confined area and that survey control passed between the RTS units is lost. If a tiltmeter fails it is limited to a single point resulting in a much lower impact on the overall system. There were 258 tilt sensors in total which are sectioned off into eight separate communications gateways. Even if an entire gateway fails, it would only take down 1/8 of the system, minimising impact further.
Another reason for not using an RTS system in this instance is that they are power intensive, which makes batteries an inadequate solution meaning that cabling would have been required. Any cabling works would have resulted in a lengthier installation process which could not be afforded due to the time constraints and pre-booked possessions. Control panels which need to be placed within 25m of the actual RTS itself would also have needed to be installed inside the tunnel in a location only accessible during isolated possessions. The required placement would also have meant the blocking of one of the two emergency walkways, which would not have been approved.
In comparison, the tiltmeter sensors have a battery life of two to three years if set to an hourly monitoring frequency and, with careful management, the battery life could be extended further. Since the tiltmeter system is both wireless and battery powered, the cabling issue was resolved. The gateway units used to gather data from the tiltmeters required connection to mains power but, as these were situated in the access shaft, with round the clock accessibility, there is no issue with that. Tiltmeters use long-range LoRa technology requiring no cables and connect via a 4G router located at ground level in the head house, removing the need for cabling inside the tunnel.
Using wireless tilt sensors also meant that there was no need for any enclosures in the tunnel, thus not blocking any emergency escape routes. The tilt sensors themselves are of a sufficiently low profile as not to interfere on either walkway.
The final advantage of the cable free tiltmeters is that there is no requirement to electrically bond any of the equipment to ground, as there would have been with the RTS equipment. This avoids expensive design and consultation work, additional isolated possessions and expensive qualified electrical sub-contractor attendance.
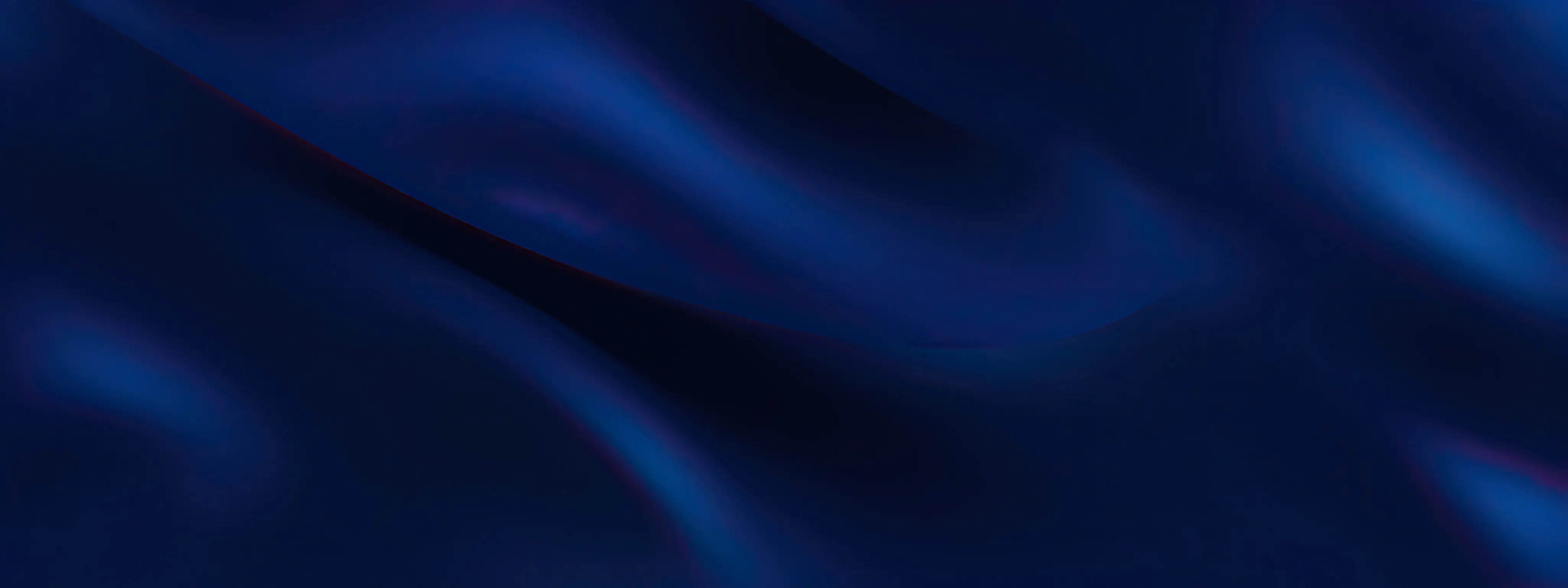
Case Study
Track trolley survey
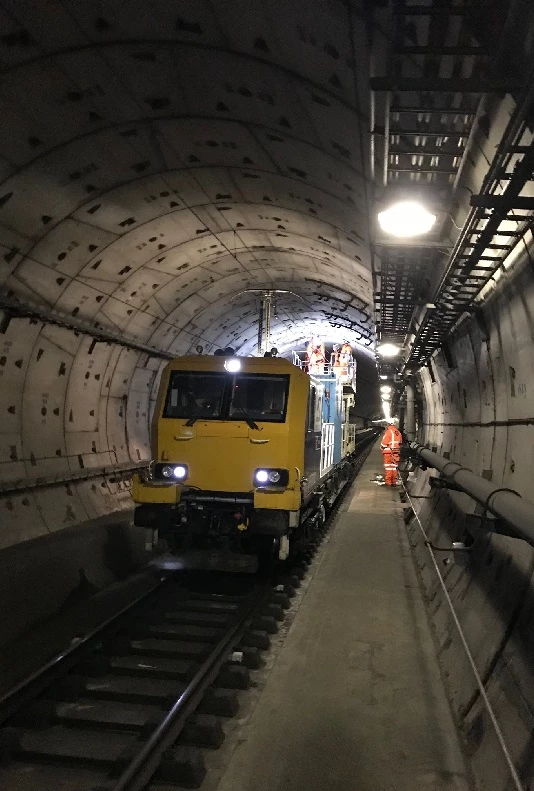
In addition to the extensive automated monitoring system, track trolley surveys are required, being carried out at 6-month intervals to confirm cant and twist, prior to, during and post the associated construction works.
The Amberg GRP 1000 track trolley used for the geometry surveys is a lightweight system that can be dismantled to small parts and carried onto the site by hand via the access route from the Ripple Lane Portal. It does not require isolation of the overhead lines which means it can be used during standard Possessions/Line Blocks, at shorter notice.
In addition to the extensive automated monitoring system, track trolley surveys are required, being carried out at 6-month intervals to confirm cant and twist, prior to, during and post the associated construction works.
The Amberg GRP 1000 track trolley used for the geometry surveys is a lightweight system that can be dismantled to small parts and carried onto the site by hand via the access route from the Ripple Lane Portal. It does not require isolation of the overhead lines which means it can be used during standard Possessions/Line Blocks, at shorter notice.
Verification surveys
At the same time as the cable free tiltmeters were installed, a system of 3D monitoring prisms was also installed adjacent to each tilt meter, to allow for verification of the tilt sensor data by means of manual survey. The verification surveys will be undertaken during the same accesses as those arranged for the track geometry trolley surveys and will include for measurement of the height of the Overhead Electrification Equipment cables as well.
Correlation survey
In addition to the above works, SOCOTEC Monitoring were also commissioned to undertake a correlation survey on the site, to tie in the positions of the below ground tunnel assets and monitoring points to the above ground work site survey grid. This involved traversing control from known points across the surface, along the railway to the tunnel portals and then back nearly 1km to the monitored zone along the tunnels.
Data visualisation
Data from all sensors is uploaded to and visualised by Calyx OMS, SOCOTEC Monitoring’s online data visualisation platform. Plans and plots of data from the site including track and tunnel profiles, convergence plots, cant, twist and rotational deformation are all viewable over the Calyx website, and additional plots can also be added for, particular parameters, by either the end users or SOCOTEC Monitoring, on request. Data from the all formats, including track trolley surveys, tilt sensors and manual verification is cross-referenced against previous data to detect any discrepancies or changes which then allows for engineering decisions to be made and for any necessary adaptations of the construction process to be made in response to observed displacements.